Understanding the Two Cylindrical One Ball Bearing Configuration in Motors
Introduction
In our previous article, we explained the application of a one cylindrical one ball bearing in electric motors. Have you ever wondered why some motors rely on a specific bearing setup known as the “two cylindrical one ball” structure? This configuration, featuring two cylindrical roller bearings and one deep groove ball bearing, is a staple in medium to large motors. It’s not just a random choice—it’s a carefully designed solution to balance load handling and shaft positioning.
In this article, we’ll explore what this structure is, why it’s used, how it works, and the critical details you need to get it right.
What is the Two Cylindrical One Ball Structure?
The “two cylindrical one ball” configuration is a motor bearing setup that combines two cylindrical roller bearings (typically NU or N series) with one deep groove ball bearing (or occasionally a four-point contact ball bearing). Here’s the basic idea:
-
Cylindrical Roller Bearings: These handle heavy radial loads thanks to their line-contact design, where rollers meet the raceway over a larger surface area. However, they can’t manage axial (thrust) loads, making them ideal as non-locating bearings.
-
Deep Groove Ball Bearing: This steps in as the locating bearing, managing axial loads and keeping the shaft aligned.
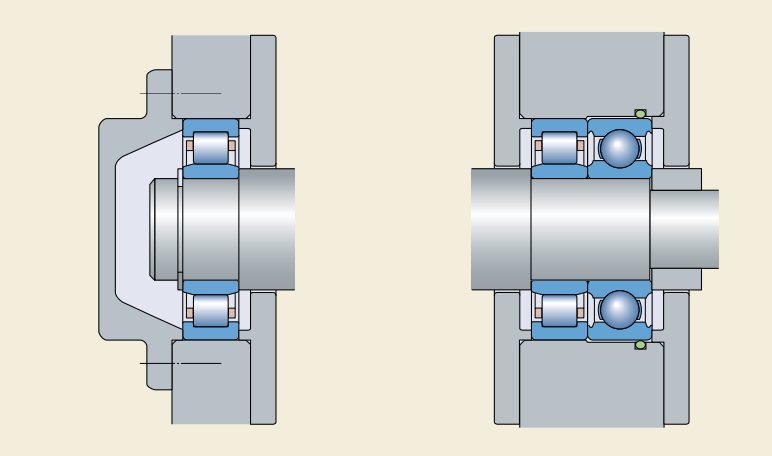
Picture it like a team effort: the cylindrical bearings are the muscles, lifting the radial load, while the ball bearing is the guide, ensuring everything stays on track. In a typical setup, one end has a single cylindrical bearing (non-locating), while the other pairs a cylindrical bearing with a ball bearing (locating) to secure the shaft in space.
Why Do Motors Use This Configuration?
So, why choose this setup over, say, a simpler all-ball-bearing design? It boils down to two key factors: load handling and positioning.
Load Handling
Cylindrical roller bearings shine when radial loads get heavy. Unlike ball bearings, which use point contact and have limited load capacity, cylindrical bearings distribute the load across a line, making them perfect for motors with significant radial stress. If a motor’s radial load exceeds what deep groove ball bearings can handle, swapping in cylindrical bearings becomes a no-brainer.
Positioning
Here’s the catch: cylindrical roller bearings don’t handle axial loads. If you used two of them alone, the shaft could slide axially, causing chaos. That’s where the deep groove ball bearing comes in—it locks the shaft in place axially. In short, the cylindrical bearings carry the radial weight, while the ball bearing ensures the shaft doesn’t wander.
This combo is a direct response to motors needing robust radial support without sacrificing precise axial control—think of it as the best of both worlds.
How Does the Two Cylindrical One Ball Bearing Structure Work?
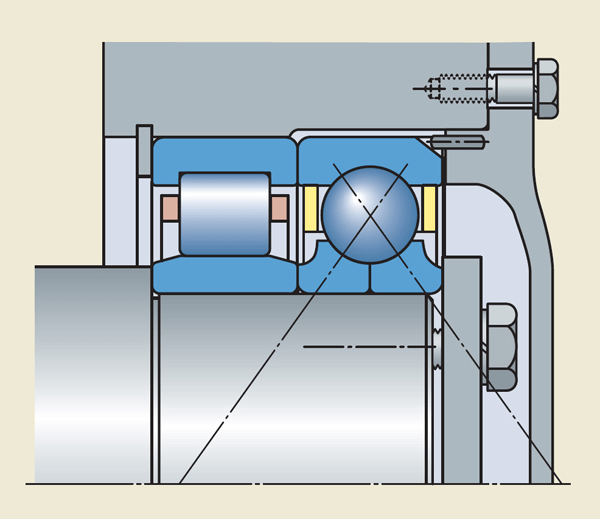
Let’s dive into the mechanics. In a single-shaft motor, the bearing system needs at least two support points to stabilize the shaft in space. The “two cylindrical one ball bearing” setup splits the job smartly:
-
Non-Locating End: A single cylindrical roller bearing supports the shaft radially but allows axial float within the bearing itself.
-
Locating End: A cylindrical roller bearing and a deep groove ball bearing work together. The cylindrical bearing takes the radial load, while the ball bearing handles axial positioning.
The result? The shaft is free to rotate but fixed in all other directions. For larger motors or those with some axial load, the deep groove ball bearing might be swapped for a four-point contact ball bearing, which offers even greater axial capacity—though it still avoids radial loads.
Key Considerations for Using the Two Cylindrical One Ball Bearing Structure
This setup isn’t foolproof—get the details wrong, and you’ll face issues like noise, wear, or even failure. Here are the must-know considerations:
Ball Bearing’s Role: Positioning, Not Load-Bearing
The deep groove ball bearing is there to position the shaft, not to carry radial loads. Applying radial force to it can lead to premature wear. To prevent this, designs often “release” the ball bearing radially—think of it as letting it float slightly while securing it axially with clamping or an O-ring to stop outer race creep.
Cylindrical Bearings and Axial Limits
Cylindrical roller bearings (NU or N types) can’t handle axial loads, so don’t expect spring preloads to quiet them down—it won’t work. Their strength lies solely in radial support.
Tolerance and Fit Matters
Unlike deep groove ball bearings, cylindrical roller bearings need a tighter outer race fit to counter creep from circumferential rolling. At the locating end, avoid identical fits for both bearings—loosen the ball bearing’s radial fit to ensure the cylindrical bearing takes the load.
Lubrication Challenges
With two bearings side-by-side at the locating end, lubrication gets tricky. For grease lubrication, feed fresh grease from the cylindrical bearing side (the main load-bearer) and let it exit through the ball bearing. This ensures both get lubed, with priority on the harder-working roller bearing.
Clearance and Noise
Bearing “whistling” is a common complaint. Choosing the right clearance—like C3L for cylindrical bearings instead of standard C3—can reduce noise by keeping working clearance tighter. Check manufacturer catalogs to confirm optimal settings.
Installation and Maintenance
Place the locating end (ball and roller pair) on the drive or non-drive side based on access needs. The ball bearing’s radial gap makes it easier to remove, so positioning it outward simplifies disassembly.
Common Pitfalls and How to Avoid Them
Engineers sometimes stumble with this setup—here’s what to watch for:
-
Overloading the Ball Bearing: Replacing cylindrical bearings with ball bearings across the board (e.g. three ball bearings) ignores radial load limits and invites failure.
-
Outer Race Creep: Relying solely on axial clamping won’t stop the ball bearing’s outer ring from moving—add an O-ring for reliability.
-
Ignoring Flexure: In large motors, heavy radial loads can bend the shaft, stressing cylindrical bearings sensitive to misalignment. Adjust bearing selection if needed.
When to Use—or Skip—This Configuration
The “two cylindrical one ball bearing” structure thrives in mid-to-large motors with high radial loads and moderate axial demands. For small motors, it’s overkill—simpler setups suffice. In very large motors, sourcing big deep groove ball bearings can get costly or impractical, pushing designers toward alternatives.
Wrapping Up: Why It Matters
The “two cylindrical one ball bearing” bearing configuration isn’t just a tradition—it’s a proven solution for balancing strength and stability in motors. By pairing cylindrical roller bearings’ radial prowess with a ball bearing’s axial precision, it tackles real-world challenges head-on. But success hinges on the details: proper load distribution, smart fits, and thoughtful lubrication.
What’s your experience with this setup? Have you run into quirks or tweaks that made it work better? Contact us!—because in motor design, the devil’s always in the details.