The Advantages of Oil-Air Lubrication: Why It’s a Game-Changer for Bearings
Introduction
Oil-air lubrication is revolutionizing how we maintain bearings and other moving parts. Not only does it improve the working environment for bearings, but it also brings significant benefits in cooling, cost savings, energy efficiency, and environmental protection. Curious about how it works and why it’s so effective? Let’s dive into the top advantages of oil-air lubrication and see why it’s becoming the go-to choice for many industries.
What is Oil-Air Lubrication?
Before we explore its benefits, let’s quickly recap what oil-air lubrication is. Unlike traditional methods that rely on oil mist or grease, oil-air lubrication uses a precise mix of compressed air and small amounts of oil to lubricate bearings. This creates a thin, continuous oil film while using minimal lubricant. Now, let’s see why this approach is so advantageous.
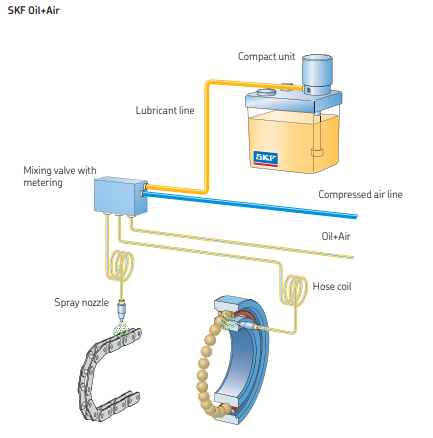
Top 10 Advantages of Oil-Air Lubrication
Simplified Piping
-
Why it matters: Oil-air systems use straightforward, low-pressure pipes that are easy to install and maintain.
-
Comparison: Unlike oil mist systems (which require high-to-low conveyance) or oil circulation systems (which need return pipes), oil-air lubrication keeps things simple.
-
Benefit: Fewer leaks, easier setup, and no special routing requirements.
Low Energy Consumption
-
Why it matters: Oil-air lubrication delivers exactly the right amount of lubricant—no more, no less.
-
Comparison: It uses just a fraction of the lubricant compared to oil mist (several times less), grease (tens of times less), or oil circulation systems (which often waste oil through leaks).
-
Real-world example: A steel mill’s bar production line cut oil consumption to one-fourth after switching to oil-air lubrication, and bearing burnouts vanished.
Minimal Environmental Impact
-
Why it matters: The oil and air don’t mix or atomize, so the air released from the bearing is clean.
-
Benefit: No oil mist in the air, making it safer for workers and the environment.
-
Key takeaway: Precision lubrication means less waste and cleaner operations.
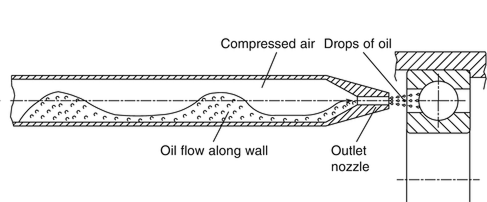
Low Maintenance Costs
-
Why it matters: With fewer moving parts and lower energy use, oil-air systems are cheaper to run.
-
Maintenance needs: Just clean the air filter and high-pressure filter regularly, and top up the oil tank.
-
Long-term savings: Longer component life and fewer repairs mean lower overall costs.
Cooler Bearings
-
Why it matters: Compressed air acts as a natural coolant, carrying away heat.
-
Cooling effect: In high-temperature settings, bearings can run 30-150°C cooler; in milder conditions, 10-40°C cooler.
-
Added bonus: The positive pressure (0.1-0.3 bar) inside the bearing housing keeps out water, chemicals, and debris.
-
Case study: A steel mill’s H-beam rolling mill saw bearing temperatures drop by 30-150°C and bearing life increase by 3-6 times after adopting oil-air lubrication.
High Lubrication Efficiency
-
Why it matters: The gas-liquid film in oil-air lubrication enhances load-bearing capacity and reduces friction.
-
How it works: A slow, steady stream of fresh oil ensures the bearing always has optimal lubrication.
-
Result: Bearings last 3-6 times longer than with other methods, saving on spare parts and downtime.
Quick Return on Investment
-
Why it matters: Oil-air systems pay for themselves fast—often within 6 months to a year.
-
Reason: Lower lubricant use, fewer repairs, and extended equipment life add up quickly.
Versatile Applications
-
Why it matters: Oil-air lubrication works for a wide range of components, including rolling bearings, open gears, chains, and rails.
-
Ideal for: High-temperature, high-speed, heavy-load, or ultra-low-speed environments, and areas exposed to water or chemicals.
Fewer Moving Parts
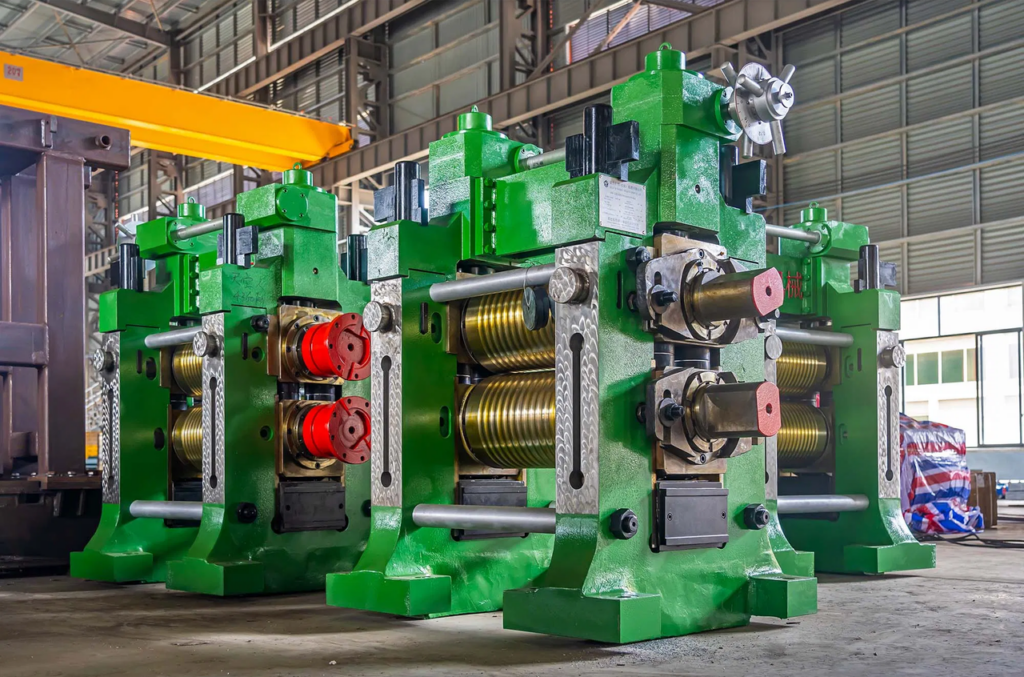
-
Why it matters: Simplicity equals reliability. Oil-air systems have only three moving parts: the oil pump, progressive distributor, and solenoid valve.
-
Benefit: Fewer components mean less wear and tear, leading to more stable and dependable operation.
Advanced Monitoring and Control
-
Why it matters: Oil-air systems come with comprehensive PLC controls and user-friendly interfaces.
-
Features: Monitor oil, air, and oil-air mixtures; switch between local, remote, or test modes; and get real-time status and fault alerts.
-
Integration: Easily connects to your equipment’s control system for seamless operation.
Why Choose Oil-Air Lubrication?
Oil-air lubrication isn’t just another option—it’s a smarter, more efficient way to keep your bearings running smoothly. From reducing energy use and maintenance costs to extending bearing life and protecting the environment, its advantages are clear. Whether you’re dealing with extreme temperatures, high speeds, or harsh conditions, oil-air lubrication delivers precision and performance where it counts.
Ready to make the switch? Explore how oil-air lubrication can transform your operations and cut costs. Have questions or success stories? Share them below—we’d love to hear from you!