Mastering Mechanical Seals in Vertical Rolling Mills: Design, Installation, and Maintenance
Introduction
Vertical rolling mills are vital in the metal processing industry, and their mechanical seals are key to ensuring smooth operation and long-lasting bearings. Poorly designed or maintained seals can lead to leaks, downtime, and costly repairs.
In this guide, we’ll explore the technical requirements, design principles, and practical strategies for installing and maintaining mechanical seals in vertical rolling mills. Whether you’re a technician or a manager, this article will equip you with the knowledge to keep your equipment running reliably.
Why Mechanical Seals Matter in Vertical Rolling Mills
Ever wondered what keeps a vertical rolling mill humming along without leaks or bearing failures? It’s the mechanical seal.
They protect bearings from contaminants, prevent lubricant loss, and maintain operational efficiency. But here’s the kicker: they need precise design, careful installation, and regular upkeep to perform at their best. Let’s dive into the details.
Technical Requirements for Mechanical Seal Installation
Proper installation sets the foundation for seal performance. Here are the critical technical specs you can’t afford to overlook:
Shaft Bending: Keep It in Line
-
What it is: The degree of curvature along the shaft’s length.
-
Why it matters: A bent shaft stresses the seal unevenly, risking leaks or breakdowns.
-
Standard: Keep shaft bending within 0.05mm for optimal performance.
Gland Requirements: Precision Counts
-
What it is: The gland secures the seal in place.
-
Why it matters: Misalignment here throws everything off.
-
Key tolerances:
-
Concentricity with the shaft: 0.05mm.
-
Perpendicularity of the gland’s contact surface: 0.03-0.05mm.
-
Coupling Requirements: Smooth Connections
-
What it is: Couplings link the shaft to the drive system.
-
Why it matters: Poor alignment causes vibrations and noise.
-
Tolerances:
-
Gear couplings: 0.08-0.10mm.
-
Flexible couplings: 0.05-0.06mm.
-
Rotor Runout: Reduce the Wobble
-
What it is: The rotor’s side-to-side movement during operation.
-
Why it matters: Excessive runout wears out seals and bearings.
-
Limit: Keep it under 0.06mm near the seal ring.
Axial Movement: Control the Shift
-
What it is: The shaft’s back-and-forth motion.
-
Why it matters: Too much movement grinds down the seal.
-
Range: Stay within ±0.5mm.
Designing Mechanical Seals for Vertical Rolling Mills
A smart design keeps your seals—and your mill—running smoothly. Here’s how two common seal types work:
Labyrinth Seals: The Leak Blocker
-
How it works: Multiple grooves create a maze-like path, stopping liquids, gases, and dust from reaching the bearing.
-
Extra protection: Add O-rings on both sides of the seal cover for an airtight seal.
labyrinth-seal
Lip Seals: The Tight Fit
-
How it works: A flexible lip presses against the shaft to block leaks.
-
Material choice: Use 42CrMo for the positioning sleeve, heat-treated for durability and wear resistance.
-
Clever feature: A groove near the roller side collects leaking oil and redirects it back to the seal, keeping lubrication intact.
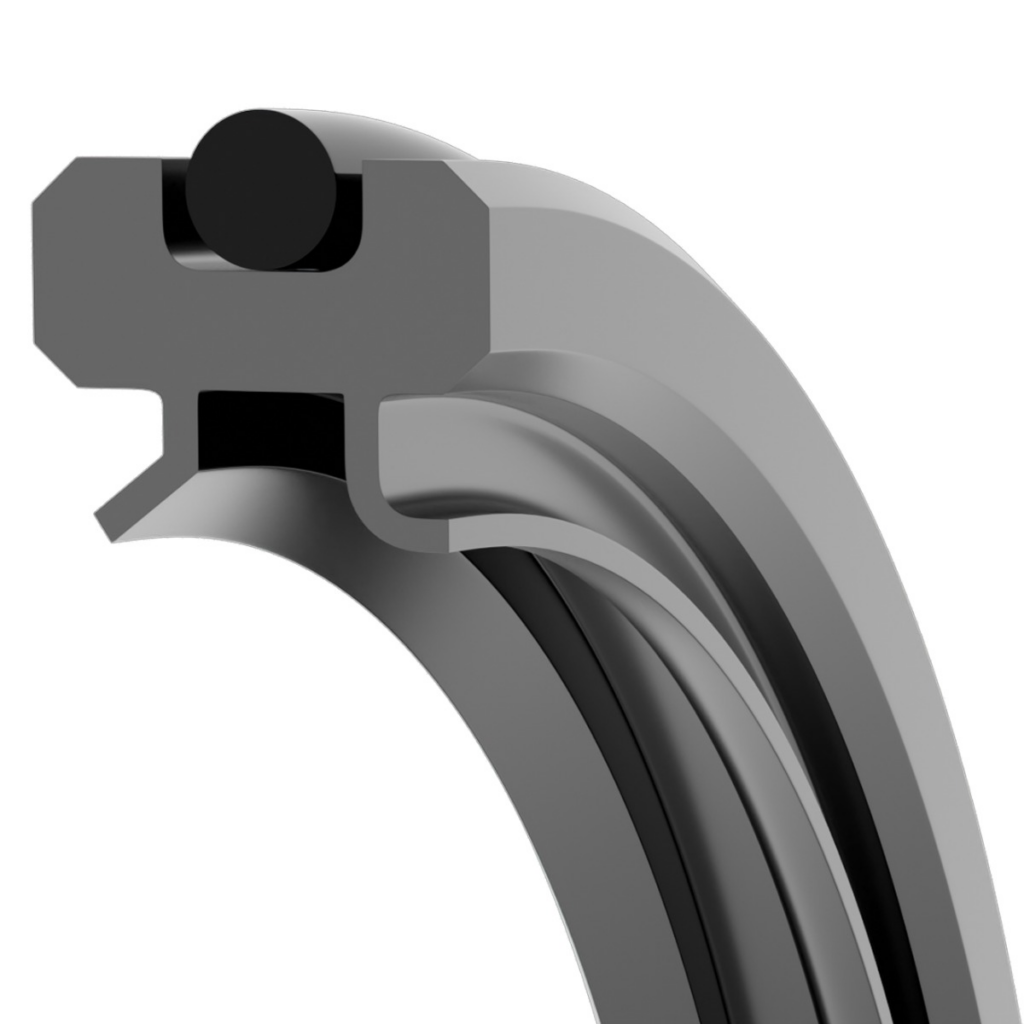
Installing Mechanical Seals: Your Step-by-Step Guide
Ready to install? Follow these steps to ensure your mechanical seal performs flawlessly:
-
Pre-Check Everything
-
Verify all parts meet design specs. Fix or replace anything that’s off.
-
-
Clean and Lubricate
-
Apply a light coat of lubricant to the roll surface.
-
Wipe down components to remove dust and debris.
-
-
Assemble with Care
-
Install the labyrinth seal and O-rings first, followed by the positioning sleeve and lip seal.
-
Align everything per the blueprint—precision is non-negotiable.
-
-
Test It Out
-
Inspect for loose parts or misalignment after assembly.
-
Run a performance test to confirm the seal holds tight.
-
Maintaining Mechanical Seals: Stay Ahead of Trouble
Routine maintenance keeps your seals—and your mill—in top shape. Here’s what to do:
Daily Maintenance
-
Pre-Startup Check: Ensure all seal components are secure and correctly positioned.
-
Quick Test: Spin the roll by hand. It should turn smoothly with no strange noises.
Regular Inspections
-
Lubrication: Monitor oil levels and check for leaks.
-
Listen Closely: Grinding or squeaking? That’s a sign of seal or lubrication issues.
Troubleshooting Common Seal Issues
Problems happen. Here’s how to fix two frequent headaches:
Issue 1: Overheating and Smoking
-
Cause: Seal failure or low lubrication.
-
Fix:
-
Stop the machine immediately.
-
Inspect the seal for damage or misalignment.
-
Check and refill lubrication if needed.
-
Replace the seal if the problem persists.
-
Issue 2: Water in the Bearing Housing
-
Cause: Seal failure or sloppy installation.
-
Fix:
-
Shut down the mill and check all seal components.
-
Tighten or replace loose or damaged parts.
-
Inspect the bearing housing for additional leaks.
-
Conclusion: Seal Success for Your Vertical Rolling Mill
Mechanical seals may be small, but their impact is huge. With the right design, careful installation, and consistent maintenance, you’ll prevent leaks, protect bearings, and boost your vertical rolling mill’s efficiency. Pay attention to the details—choose quality seals, follow precise installation steps, and monitor performance regularly. Your reward? A reliable mill that powers your operations for years.
Got a tip or question about mechanical seals? Share with us—we’d love to hear from you!