High-Performance Motor Insulated Bearings-TFL
Introduction: The Revolution of Motor–Insulated Bearings
With the development of industry, especially in the application of equipment such as electric motors, conventional bearings cannot withstand the effects of electromagnetic fields generated by the passage of electric current, resulting in damage. As a result, motor-insulated bearings came into being. Modern motor insulated bearings are sprayed with insulating laminates on the outer surface, which can withstand voltages up to 3000VDC and can work stably in special environments such as high temperature, high pressure, and strong corrosion. This progress not only improves the service life of the bearings but also broadens their scope of application, including wind turbines, hydro generators, thermal generators, and other power industry facilities, as well as internal combustion locomotive traction motors and other railroad facilities.
How Motor Insulated Bearings Work: Technological Breakthroughs
Electric motor insulated bearings are coated with a layer of 50—-200μm thick ceramic coating on the inner or outer ring of the bearing based on the principle of cutting off the current circuit, which is responsible for the function of electrical insulation. The coating can resist the electric jumping fire generated under the voltage of 1,000V, and the thicker coatings can resist the high-voltage discharge of more than 1,000V. It is further treated to be unaffected by humidity and moisture.
Limitations of conventional bearings
The limitations of conventional bearings are mainly reflected in their materials and the environment in which they are used; for example, they are prone to wear and even fail in high temperature, high speed or corrosive environments. Conventional bearings are usually made of alloy steel, such as carbon steel, and do not have insulating properties, so they cannot withstand the current erosion in modern industrial motors. In electric motors and generators, there are circuit currents and induced currents between the body, bogie, and axle. During bearing rotation, when there is current passing through the bearing, it will break through the very thin oil film in the rolling contact part, generate sparks, and cause localized melting damage on the contact surface and galvanic corrosion. Resulting in bearing failure. In addition, the hardness of the rolling surface decreases and is prone to wear, thus directly affecting the performance and life of the motor and even the host. Therefore, it is very necessary to research and develop insulated bearings for electric motors and generators.
Regardless of whether the bearings are subjected to direct or alternating current (frequencies below MHz), we always find the same form of damage inside the bearings. In most cases, we find uniform dark grey marks on the raceway and rolling element surfaces. Galvanic gouge marks are continuous periodic gouge marks on the raceway surface in the running direction. This type of phenomenon is mostly caused by the passage of electric current through the bearing. Only with a scanning electron microscope (SEM), it becomes obvious that almost all damaged surfaces are densely populated with pits and μm-sized welded joints, which confirms that an electric current is passing through the bearing.
Innovative design of TFL insulated bearings
TFL insulated bearings use a special spraying process to spray insulating coatings on the inner diameter surface, outer diameter surface and end surface of the bearings to avoid the galvanic corrosion effect of induced current on the bearings to prevent the current from damaging the lubricating grease, rolling body and raceway, and to improve the service life of the bearings.
Two different materials are used for TFL high-efficiency insulated bearings, which are made into insulators by the plasma spraying preparation process.
- Spraying bearing parts with insulating materials such as oxides and resins to make them insulated bearings.
- Insulated bearings are made with nitride-insulating ceramics.
Advantages of insulated bearings manufactured by plasma spraying:
- Good bonding strength: The high-speed performance of plasma spraying ensures that the bonding strength of the bearing surface is greater than 30MPa, thus ensuring that the coating is durable.
- Small working heat influence: Due to the special process parameters, the melted particles are rapidly cooled and solidified when sprayed on the surface of the collar, which can keep the bearing surface at about 100℃, eliminating the deformation influence brought by high temperature to the bearing.
- Professional sealing technology: The insulated bearings are coated and then subjected to a sealing technique that penetrates about 20% of the thickness of the coated layer.
Applications of Motor Insulated Bearings: From Industry to Aerospace
Motor-insulated bearings are widely used in several industries because of their unique insulating properties. The following are their main areas of application:
Motors for heavy industry: the heart of efficiency improvement
The use of motor-insulated bearings in heavy industrial equipment is central to efficiency gains. In high-power explosion-proof motors, especially in compressors and other equipment, as well as cranes, textile machinery, printing machinery, ironmaking equipment, steelmaking equipment and other high-power variable frequency motors, motor insulated bearings through its high electric resistance, effectively avoid current damage to the bearings, to meet the insulating requirements of bearings in a variety of power equipment, to ensure the normal operation of the equipment.
Wind power: a reliable partner for renewable energy
In wind power generation equipment, the wind turbine spindle bearing is one of the core components that supports the wind turbine rotation power generation, especially in the wind turbine, where the spindle and gearbox play a key role. Wind power generation equipment is in a special working environment, such as rain, wind sand, salt spray and other harsh natural conditions, as well as the complex loads of fan hubs, paddles and wind loads. The application of insulated bearings, especially the wind turbine special insulated bearings 6328mc3, can withstand voltages of up to 1000V DC, effectively preventing damage to bearings from shaft currents, ensuring that they are still able to work stably in complex and harsh environments, and safeguarding the stable operation of wind power generation equipment.
Electric Vehicles: Powering the Future of Transportation
In electric vehicles, the main motor is usually around 100KW, and such motors must use electrically insulated bearings or adopt other insulating structures to ensure that shaft currents do not flow. In new energy vehicles, the motor bearings rotate at higher speeds compared to conventional bearings, requiring more wear-resistant materials, and due to the changes in electromagnetic fields caused by the alternating currents in the motor, better insulation is required to minimize galvanic corrosion resulting from the discharge of the bearings. Therefore, ceramic bearings, especially silicon nitride hybrid ceramic bearings, are widely used in the field of new energy vehicles due to their excellent insulation and wear-resistant properties. For example, SKF 625-2RZTN9/HC5C3WTF1, SKF 608-2RSL/HC5C3WT.
Aerospace: Excellence in Extreme Challenges
Aero-engine insulated bearings not only support the structure and motion system of the vehicle but also resist vibration and shock, reduce friction and wear, and their lightweight design reduces the weight of the entire vehicle and improves payload capacity and fuel efficiency. As aerospace technology continues to develop, the demand for higher-grade aerospace bearings continues to increase to meet the more demanding requirements of space missions.
Smart manufacturing: a key component of Industry 4.0
Insulated bearings play a pivotal role in the semiconductor industry chain. Among them, silicon carbide bearings, with their excellent performance, occupy an indispensable position in semiconductor equipment. It can withstand high temperatures, high speeds, heavy loads, and other harsh working conditions, ensuring stable operation and long equipment life. For example, in the smart factory motor insulation bearing applications, silicon carbide bearings can achieve precise and stable motion control to ensure that robots can accurately grasp and carry semiconductor devices; in LCD screen transfer equipment and HD substrate transfer equipment, silicon carbide bearings are able to provide high-speed, smooth rotary motion to ensure stable operation and efficient production of the equipment.
Advantages of TFL Insulated Bearings
TFL, as a leading bearing manufacturer, is committed to developing advanced insulated bearing technology and electrically insulated bearing systems. The main advantages of TfL’s motor bearings are summarized in the following areas:
Improved equipment reliability
Isolating current and preventing galvanic corrosion: TFL insulated bearings can avoid the galvanic corrosion effect of induced current on bearings, reduce the risk of bearing damage due to galvanic corrosion, and ensure stable operation of equipment.
Extended service life
- High temperature and corrosion resistance: TFL motor insulation bearings adopt special materials and manufacturing processes, making them perform better in high temperature and corrosion resistance. They can operate normally in harsh environments and significantly prolong the service life of the bearings and equipment.
- Reduce the number of repairs: the use of TFL insulated bearings can reduce the number of equipment downtime and repairs caused by bearing failures, reduce maintenance costs and improve the overall economic efficiency of the equipment.
Reduced maintenance costs
Reduced failure rate and maintenance costs: TFL insulated bearings significantly reduce the failure rate of bearings by isolating the current and preventing galvanic corrosion and other measures to reduce equipment failure and downtime losses due to bearing damage and, therefore, can save users a lot of maintenance costs and downtime losses.
Technical characteristics
- Special spraying process: TFL insulated bearings adopt a special spraying process, spraying and plating a high-quality coating on the outer surface of the bearings, which has a strong bonding force with the substrate and good insulating properties. This coating process not only improves the bearings’ insulating properties but also enables them to resist the effects of moisture and humidity and maintain long-term stability.
- High Insulation Voltage: The coating formed on the surface of the outer ring or inner ring of TFL insulated bearings can withstand high voltages (e.g., up to 1,000V DC or higher), ensuring that good insulation properties can be maintained even in high-voltage environments.
Choosing the Right Motor Insulated Bearings: Expert Guide
With the development of modern industry, the application and importance of insulated bearings for electric motors have received widespread attention. The world also has a number of outstanding motor insulated bearing manufacturers with advanced insulated bearing manufacturing technology, and high-quality motor insulated bearings provide us with more choices.
SKF INSOCOAT Motor Insulated Bearings
SKF has developed the INSOCOAT insulated bearing series. These bearings have a specially coated outer ring with an electrically insulating layer and a breakdown voltage of up to 1,000 V. The bearings have an electrically insulating layer and a high breakdown voltage.
VL0241 | VL0246 | VL2071 | VL2074 | |
---|---|---|---|---|
Resistive | Minimum 50 MW | > 150 MW | Minimum 50 MW | > 150 MW |
Breakdown voltage (Maximum working voltage) | 1 000 V DC | 3 000 V DC | 1 000 V DC | 2 000 V DC |
The following is a partial catalogue of SKF insulated bearings:
Designation | Principal dimension | Basic load ratings | Speed ratings | ||||
---|---|---|---|---|---|---|---|
dynamic | static | Reference speed | Limiting speed | ||||
d[mm] | D[mm] | B[mm] | C[kN] | Co[kN] | r/min | r/min | |
6314 M/C3VLO241 | 70 | 150 | 35 | 104 | 68 | 9500 | 9000 |
6315-Z/C3VL0241 | 75 | 160 | 37 | 119 | 76.5 | 9000 | 5600 |
6216/C3VLO241 | 80 | 140 | 26 | 72.8 | 55 | 9500 | 6000 |
NU210ECM/C3HVA3091 | 50 | 90 | 20 | 73.5 | 69.5 | 8500 | 9000 |
NU316ECM/C3VL2041 | 80 | 170 | 39 | 300 | 290 | 4300 | 5000 |
NU315ECP/VL0241 | 75 | 160 | 37 | 280 | 265 | 4500 | 5300 |
FAG J20 Motor Insulated Bearings
FAG motor-insulated bearings are denoted by the suffixes J20AA, J20AB and J20C. FAG motor-insulated bearings can be regarded as an upgraded version of the standard uninsulated ball bearings with current passage protection. Therefore, the specifications are the same as for standard deep groove ball bearings, e.g. 6219-M-J20AA-C3 FAG has the same characteristics as the standard 6219-M-C3 FAG.
The suffixes used by FAG for their current-insulating bearings are:
- J20AA: The J20AA indicates the addition of an aluminum oxide coating on the outer ring to withstand voltages up to 3.000 V DC. As:6216.C3.J20AA
- J20AB: The J20AB indicates the addition of an aluminum oxide coating on the outer ring to withstand voltages up to 1.000 V DC. As:6224-J20AB-C3
- J20C: The J20C indicates the addition of an aluminum oxide coating on the innerring to withstand voltages up to 3.000 V DC. As:6326.M.C3. J20C
NTN MEGAOHMS Motor Insulated Bearings
NTN MEGAOHMS Insulated Bearing Series designed to counteract electrical pitting. These bearings are available in ceramic and resin types for various applications. The MEGAOHM series of insulated bearings offer the following unique advantages:
- Exhibits insulation resistance of at least 100 MΩ at 500 VDC.
- It can meet different user requirements by using a variety of insulation layer materials, high voltage resistance, and impact resistance.
- Complies with ISO 492, DIN 620 and JIS 1514.
- Aperture diameters range from 50 to 160 mm.
The following is a partial catalogue of NTN insulated bearings:
Bearing types | Bearing numbers | Boundary dimensions/mm | Basic load ratings | Collar ring numbers | ||||
---|---|---|---|---|---|---|---|---|
d | D | B | rs min | Dynamic(N/Cr) | Static(N/Cr) | |||
Cylindrical roller bearings | 7MC (n) -NU214 | 70 | 125 | 24 | 1.5 | 83500 | 95000 | HJ318 |
7MC (n) -NU314 | 70 | 150 | 35 | 2.1 | 158000 | 168000 | HJ320 | |
7MC (n) -NH322 | 110 | 240 | 50 | 3 | 360000 | 400000 | HJ322 | |
7MP2-NU314 | 70 | 150 | 35 | 2.1 | 158000 | 168000 | ||
7MP2-NU215 | 75 | 130 | 25 | 1.5 | 166000 | 195000 | ||
Deep groove ball bearings | 7MC (n) -6316 | 80 | 170 | 39 | 2.1 | 123000 | 86500 | |
7MC (n) -6324 | 120 | 260 | 55 | 3 | 207000 | 185000 | ||
7MC (n) -6230 | 150 | 270 | 45 | 3 | 176000 | 168000 | ||
7MP2-6314 | 70 | 150 | 35 | 2.1 | 104000 | 68000 | ||
7MP-6215 | 75 | 130 | 25 | 1.5 | 66000 | 49500 |
Installation and Maintenance of TFL Insulated Bearings
In the installation and maintenance of insulated bearings, one needs to pay attention to the correct steps and matters. Below is some important information about the installation and maintenance of insulated bearings:
Pre-installation preparation
Preparation of insulated bearings before mounting mainly includes the following aspects:
- Use specialized tools to avoid bearing damage caused by improper handling
- Checking the integrity of the bearing package
- Check that the dimensions of the shaft and housing correspond
- Bearings and housings need the right amount of oil
- Ensure that the installation environment is in a dry, dust-free room
- Clean installation tools to prevent dust and contaminants
- Check that there is no wobble in the bearing housing
Correct installation method
Insulated bearings are mounted in three general ways:
- Cold mounting/mechanical methods (tapping method, spiral method, mechanical pressure method)
- Hot mounting (electric induction, electric hot plate, other methods)
- Hydraulic method
Routine maintenance checks
Routine maintenance and inspection of insulated bearings requires attention to the following points:
- Cleanliness check: Cleaning of bearing surfaces and housings and mounting environment
- Lubrication status check: bearing lubricant status and lubrication mode check
- Operation status check: vibration and noise check and temperature check
- Appearance and structure check: bearing appearance and structure check whether it is intact
- Regular disassembly for inspection and cleaning
Troubleshooting
The main causes of bearing insulation failure:
- Poor lubrication: Bearings need good lubrication to reduce friction and wear during operation. If the lubricant is insufficient, of poor quality, or not replaced in time, it will lead to overheating of the bearing and increased wear and tear, which in turn will lead to insulation failure.
- Contaminant intrusion: Poor sealing or improper maintenance of bearings may allow dust, moisture, and other contaminants to enter, destroying the bearings’ insulating properties.
- Overloaded operation: Long-term overloaded equipment operation will make the bearings withstand excessive pressure and heat, accelerating the aging and damage of the insulation material.
Tips for optimizing longevity
The techniques for optimizing the service life of insulated bearings are multi-faceted, and the following are some of the key measures:
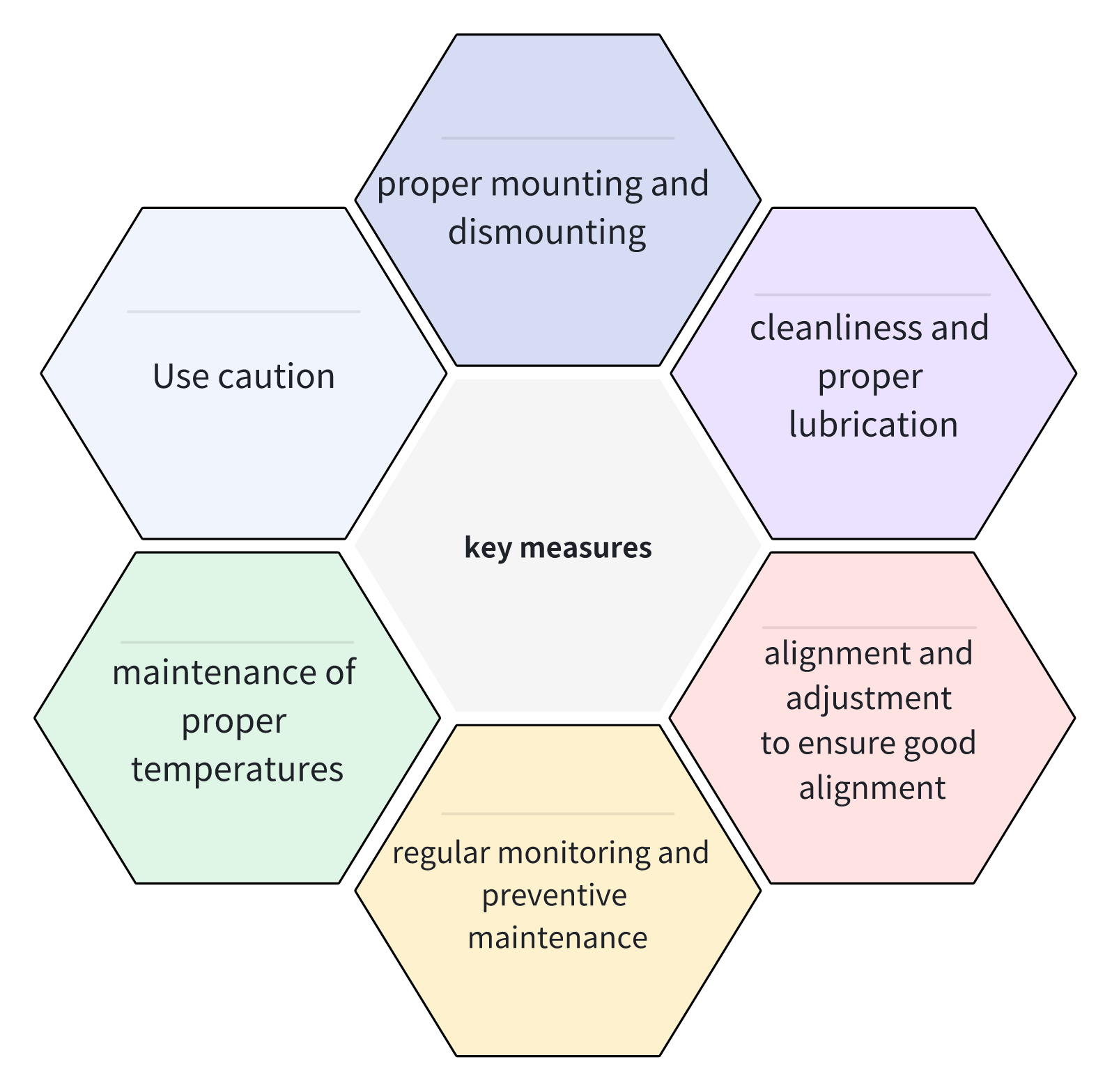
Conclusion: The Value of Investing in TFL Insulated Bearings
In terms of bearing manufacturing, TFL Insulated Bearings has advanced production equipment and technical processes. We emphasize research, development, and innovation and constantly introduce bearing products with better performance and adaptability. We have stock from more than 100 suppliers, as well as our own bearing products, professional technical support, and after-sales service. High-quality TFL bearings can help us improve production efficiency and reduce maintenance costs. We would be happy to serve you on your journey to optimize the performance of your motors!
Frequently Asked Questions
- What are motor-insulated bearings?
Motor-insulated bearings are coated with a layer of insulating material on the outer or inner ring of the bearing through a special process, which can block the passage of electric current and prevent galvanic damage. These bearings can also be made with ceramics for the rolling bodies, thus ensuring their insulating properties.
- How long can motor-insulated bearings extend the life of a motor?
The life cycle of motor bearings varies according to different working conditions, generally about 3-5 years.
- What is the proper way to replace motor bearings?
- Select appropriate bearings. The appropriate bearings, such as high-temperature, high-speed, and corrosion-resistant bearings, should be chosen according to the motor load, speed, environment, and other conditions.
- Carry out good maintenance after replacing the bearings. After replacing the bearings, pay attention to the bearings for lubrication, refueling and other maintenance work to extend the service life of the bearings.
- Check before replacement. Before replacing the bearings, the original bearings should be inspected to confirm whether they are damaged and how to replace them to better ensure the safety and stability of the motor.
- What factors need to be considered when selecting the right insulated bearing for the application?
Selecting the right insulated bearing for an application requires consideration of a number of factors, including the application scenario, environmental conditions, nature of the load, rotational speed, rotational accuracy, and centring performance.
- Do I need special tools or skills to install insulated bearings?
The mounting of insulated bearings does require special tools: special tools for mounting and dismounting bearings, heating equipment, and protective cushion covers.
Skills: Selection of appropriate installation method, precise control of installation strength and temperature, cleaning and lubrication, inspection and maintenance.