How do ball and roller bearings work? Types and durability calculation. DIN ISO 281
Bearings are used to reduce the friction between two objects that are in a linear or circular motion against each other.
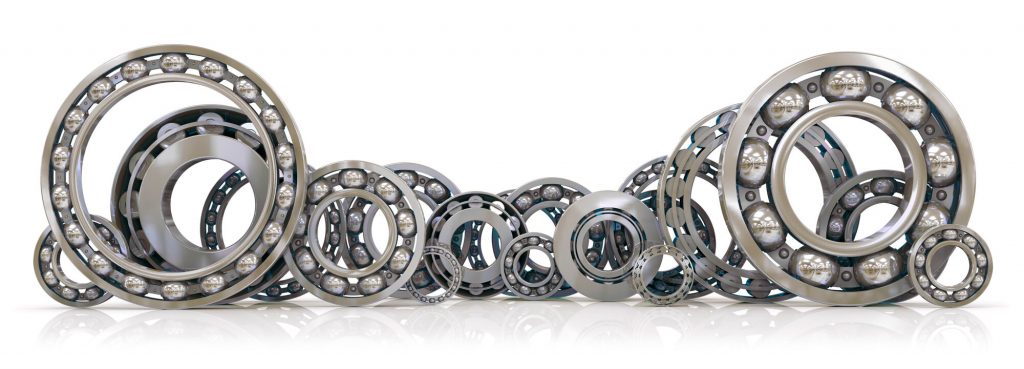
The first intuition came from Leonardo Da Vinci in his studies regarding friction. But the first patent was filed only in 1794 by Philip Vaughan of Carmarthen. Then, a Parisian bicycle mechanic named Jules Surrey patents the first ball bearing on August 3rd, 1869. This invention allows him to win the first cycling race in history: the Paris-Rouen race.
Now let’s take a closer look at a classical ball bearing. By decomposing and sectioning it, its components can be analyzed. The first elements that immediately get our attention are the steel balls. They represent the rolling elements, and they’re held together by a cage that can come in different shapes and is made of low friction materials. Then, we have the inner ring (usually the one that moves) and the outer ring, both with a groove, which can be more or less deep to make the rotary elements glide.
It is widespread for the bearing also to be shielded. The shield can be made of metal for dust protection, or it can be made of plastic, preventing liquid infiltrations. They are placed in specific locations between the two rings to protect the balls and the cage from external agents. At the same time, they can retain oil or grease inside the bearing, keeping it lubricated for its entire life cycle.
To work correctly, bearings need a specific radial and axial clearance so that when they reach the working temperature, their thermal expansion won’t lead to overtightening (which would cause the bearing’s wear), or in the worst case, even a seizure!
Ball bearings are among the most used approaches. The radial ones can be classified as single-row bearings (the most common type) or double-row bearings (which can withstand high radial loads).
Among the radial ball bearings, we also find the self-aligning bearings with two rings of balls. This type has an inner circle with two grooves placed side by side, while the outer ring has only one hemispherical groove. This system allows the inclination of the two rings’ axis during the functioning.
There are also angular contact ball bearings that have either one or two rings of spheres. They typically have an oblique position (respective to the axis of rotation) of the load line passing through the contact points between the balls and the rings. They can withstand higher radial loads and axial forces.
Finally, it should be noted that all these varieties can also have an axial configuration, to withstand a mainly axial load. They are also called thrust bearings.
The other primary type of rotary bearings is the so-called roller bearings, used when very high accuracy is required. They have the same categories: radial, angular contact, and axial bearings. But roller bearings have different shapes depending on the type: this is another difference between these and ball bearings.
Radial bearings with cylindrical rollers are the most common type. If they have small rollers, they’re called needle roller bearings, and thanks to their compactness, they are used when space is limited. They can only withstand radial loads.
There is another variety: spherical roller bearings, which have cask-shaped rollers, to include the rotation axis of the two rings.
Tapered roller bearings are an oblique version and are used in case of combined load. This type of bearings is generally used in pairs, and they usually have an inverse taper.
All these variations can also have an axial configuration to withstand an axial load mainly. They are also called thrust bearings.
Bearings are one of the most used mechanical parts, and there are many varieties of them. So it is essential to consider the area of use when choosing the correct bearing. The reference standard for bearings is DIN ISO 281, which provides a formula for the calculation of bearings’ durability: given the dynamic load coefficient of the bearing “C,” the equivalent dynamic load “P” and a specific coefficient, which is 3 for ball bearings, and ten thirds for roller bearings. The “n” allows us to obtain the durability of the approach expressed as millions of turns.
The equivalent load “P” is calculated based on the radial and the axial load, which acts on the bearing. The coefficient of the dynamic load is instead determined by the fatigue behavior of a significant lot of similar poses.
Ball bearings
Ball bearings are probably the most common type of bearing. From inline skates to hard drives, they are everywhere. These bearings can withstand radial loads and thrust loads and are usually used in applications with relatively small loads.
In ball bearings, the load is transferred from the outer ring to the ball and then from the ball to the inner ring. Since the ball is a sphere, it only touches the inner and outer rings at a tiny point, which helps it to rotate very smoothly. But this also means that the contact area carrying the load is not large, so if the bearing is overloaded, the balls will deform or squeeze, which will damage the bearing.
Roller bearing
The roller bearings shown in the figure below are used in conveyor rollers, where they must bear heavy radial loads. In these bearings, the roller is a cylinder, so the contact between the inner and outer rings is not a point but a line. This spreads the load over a larger area, allowing the bearing to withstand much larger loads than ball bearings. However, this type of bearing is not designed to handle large thrust loads.
A variant of this bearing called a needle roller bearing uses a cylinder with a minimum diameter. This allows the bearing to be installed in narrow places.
Ball thrust bearing
The ball thrust bearings shown below are mainly used for low-speed applications and cannot withstand large radial loads. Barstools and Lazy Susan turntables use this bearing.
Roller thrust bearing
The roller thrust bearing shown in the figure below can withstand larger thrust loads. They often find the gears between a car’s gearbox like a gear set and between the housing and the rotating shaft. The helical gears used in most transmissions have helical teeth-this causes thrust loads that bearings must support.
Tapered Roller Bearings
Tapered roller bearings can withstand large radial loads and large thrust loads.
Tapered roller bearings are used in automobile wheels. They are usually installed in pairs, facing opposite directions, to withstand thrust in both directions.