Cylindrical Roller Bearings vs. Ball Bearings
Introduction
Cylindrical roller bearings and ball bearings are important components widely used in machinery. They reduce friction, support loads, and allow for smooth rotation.
Although they may look similar at first glance, they are very different in structure, function, and application scenarios.
This article will introduce their main differences and how to decide which type of bearing to choose.
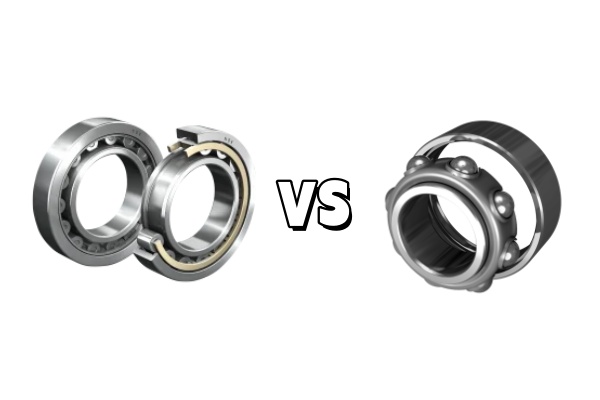
Structure of Cylindrical Roller Bearings
Cylindrical roller bearings use cylindrical-shaped rollers instead of balls.
These rollers are longer, providing a larger surface area for contact. This design allows them to handle heavier loads and withstand higher radial forces.
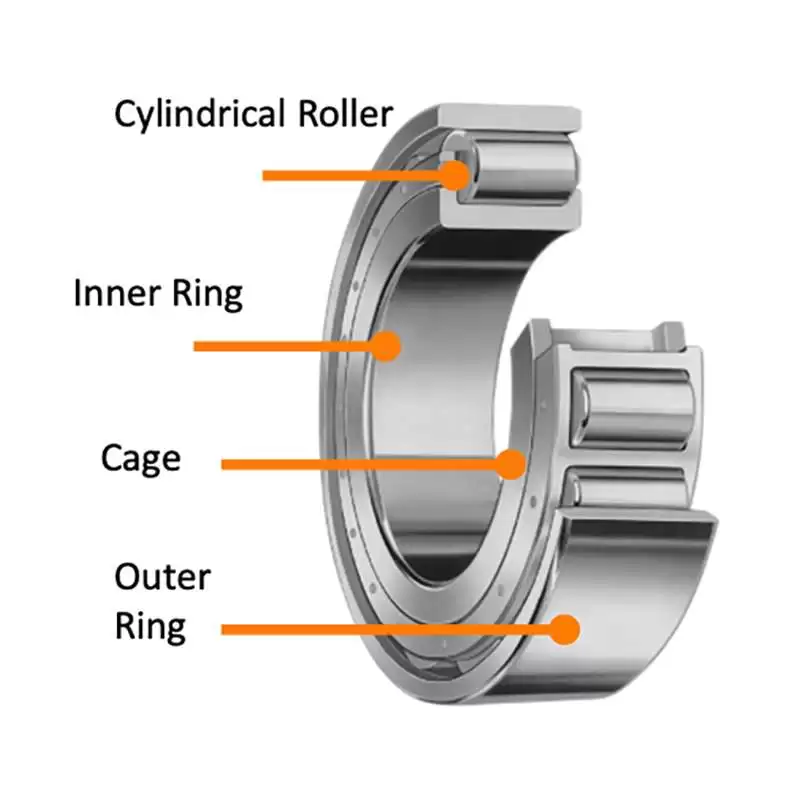
Key Features
-
Less Friction: They perform well in high-speed environments with lower friction compared to some other bearings.
-
Durable: Withstand wear and tear in demanding applications.
Typical Uses
These bearings are found in heavy machinery, such as industrial gearboxes, electric motors, and rolling mills, where durability and load capacity are priorities.
However, cylindrical roller bearings aren’t great for handling axial loads (force parallel to the shaft). If your setup involves such forces, you might need additional support bearings.
Structure of Ball Bearings
In contrast, the inner and outer raceways of a ball bearing are filled with spherical balls. The balls glide more easily because there is less friction between them.
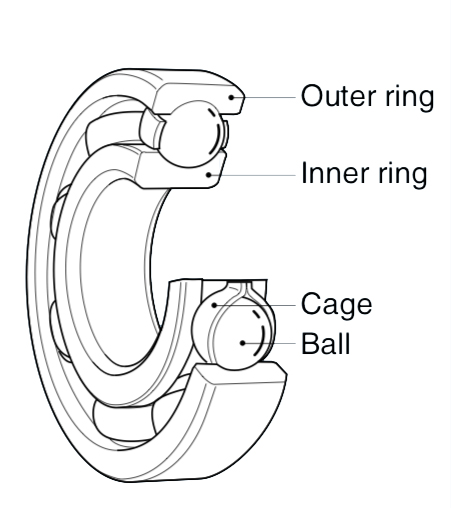
Key Characteristics of the Structure
-
Point Contact: High-speed operation is made possible by the balls’ point contact with the raceways, which reduces friction.
-
Compact Design: Ball bearings can fit into confined locations because they are usually lighter and smaller.
-
Versatility: They can handle both radial loads (perpendicular forces) and axial loads (forces along the shaft).
Typical Uses
Ball bearings are found in a wide range of applications, from bicycles and fans to precision instruments and automotive components. Their adaptability and efficiency make them an all-around favorite.
That said, ball bearings aren’t as robust for heavy loads. If your equipment faces extreme weight or pressure, they might not be the best option.
Major Differences Between Cylindrical Roller Bearings and Ball Bearings
You can make a better choice if you are aware of the distinctions between ball and cylindrical roller bearings. Here is a brief tabular summary:
Feature | Cylindrical Roller Bearings | Ball Bearings |
---|---|---|
Rolling Element | Cylindrical rollers | Spherical balls |
Contact Type | Line contact | Point contact |
Load Capacity | Higher radial load capacity | Handles both radial and axial loads |
Speed Capability | Performs well, especially under heavy loads | Better suited for very high speeds |
Durability | Excellent for demanding, high-load setups | Ideal for moderate loads and speeds |
Design Flexibility | Often separable for easier maintenance | Compact and lightweight |
Rolling Element: Cylindrical Rollers vs. Spherical Balls
The fundamental difference lies in the shape of the rolling elements. Cylindrical roller bearings use rollers, which have a larger contact surface (line contact) with the raceways. This allows them to support heavier loads compared to ball bearings, which rely on smaller, spherical balls that make point contact.
(Reference: Design of an energy efficient cylindrical roller bearing BY Acar et al., 2022)
If your machine is subjected to heavy radial forces, such as those found in gearboxes or large industrial equipment, cylindrical roller bearings are better equipped to handle the stress without wearing out prematurely.
Contact Type: Line vs. Point Contact
By using line contact, cylindrical roller bearings disperse load over a larger surface area. On the other hand, ball bearings are perfect for high-speed applications because of their point contact, which reduces friction.
Ball bearings are the obvious choice if you want smooth, quick rotation with little resistance, like in a fan or a precision instrument.
Cylindrical bearings, on the other hand, are essential in robust systems because their line contact guarantees stability under high loads.
Load Capacity: Radial and Axial
Cylindrical roller bearings are champions of radial load handling but struggle with axial forces. Ball bearings can handle a combination of both radial and axial loads, though their radial load capacity is generally lower.
If your machine experiences multidirectional forces, such as in automotive wheels or turbines, ball bearings are more suitable.
But for heavy-duty setups with significant radial force, cylindrical roller bearings will last longer and perform more reliably.
Speed Capability
Ball bearings excel in high-speed environments due to their lower-friction design. Cylindrical roller bearings, while capable of operating at moderate speeds, are more focused on load capacity than speed.
In applications like high-speed drills or electric motors, ball bearings are the preferred choice because they maintain smooth performance at elevated RPMs.
For lower-speed but high-load scenarios, cylindrical roller bearings are a more practical option.
Durability and Wear Resistance
The construction of cylindrical roller bearings is robust. In high-load, high-stress situations, their durable construction and wider contact area prolong their lives and lessen wear.
Ball bearings are more appropriate for mild weights even if they are robust in and of themselves. When reliability and long service life under heavy conditions are essential—such as in mining or construction equipment—cylindrical roller bearings provide unmatched durability.
However, for lighter machines, ball bearings deliver sufficient longevity without the extra bulk.
Design Flexibility
Because of their frequently separable parts, cylindrical roller bearings are simpler to install and maintain.
Ball bearings are perfect for precise assemblies in confined places because of their small size and low weight. Cylindrical roller bearings are simpler to use in industrial environments where routine maintenance or part replacements are necessary.
Conversely, because of the smaller size, ball bearings are favored for high-performance, tiny devices.
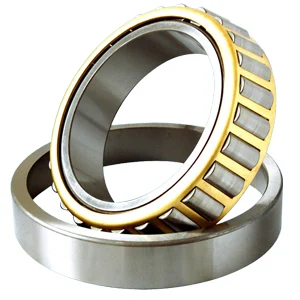
Conclusion
When deciding between cylindrical roller bearings and ball bearings, take the time to evaluate the specific operating conditions, load requirements, and space constraints of your equipment.
Selecting the right bearing is essential for performance and longevity. That’s where TFL Bearings comes in. We offer high-quality cylindrical roller bearings, ball bearings, and more—designed to keep your machinery running smoothly and efficiently.
Have questions or ready to upgrade? Get in touch with TFL Bearings today for expert guidance and premium solutions that keep your operations rolling smoothly!