Bearings and Lubrication: The Heart and Blood of Machinery
Introduction
If bearings are the heart of machinery, then lubrication is its blood.
Both are essential for reducing friction and ensuring the smooth operation of mechanical systems. Bearings—whether rolling or sliding—are designed to minimize friction through their physical structure, while lubrication achieves this through chemical means. Together, they form an inseparable duo that keeps machines running efficiently. For mechanical engineers, understanding lubrication is just as important as mastering bearing design.
In this article, we’ll explore the principles of bearings and lubrication, how speed, load, and temperature affect it, and why these factors matter for the longevity of your machinery. Let’s dive in!
Understanding Bearings and Lubrication: The Water Skiing Analogy
Ever wondered how lubrication actually works inside a bearing? Let’s break it down with a simple analogy: water skiing.
When you water ski, your skis and the water surface form a wedge-shaped space. As you move forward, water flows into this wedge, creating a lifting force that keeps you afloat. Similarly, inside a bearing, the rolling elements (like balls or rollers) and the raceway (the track they roll on) also form a wedge-shaped space. When the bearing rotates, lubricant is drawn into this space, forming an oil film that separates the rolling elements from the raceway. This reduces friction and prevents direct metal-to-metal contact.
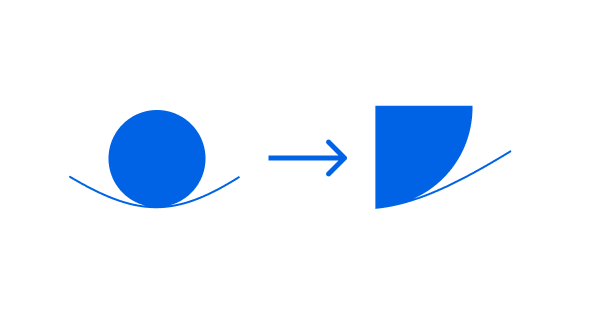
This ideal state is called hydrodynamic lubrication or full-film lubrication, where the oil film completely separates the surfaces. But what happens when the oil film isn’t fully formed?
-
Mixed lubrication: Some areas have an oil film, while others experience direct contact.
-
Boundary lubrication: No oil film at all, leading to direct metal-to-metal contact and increased wear.
Think of it like water skiing:
-
Full-film lubrication is like gliding smoothly on the water’s surface.
-
Mixed lubrication is like occasionally scraping the lake bottom.
-
Boundary lubrication is like dragging your skis across dry land—ouch!
This analogy helps us visualize how crucial lubrication is for reducing friction and wear in bearings.
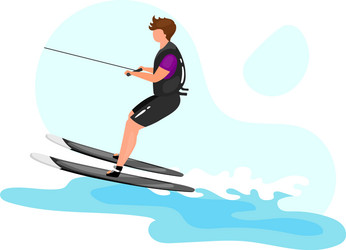
Speed Matters: How Rotation Affects Lubrication
Let’s stick with the water skiing example. If you’re standing still on your skis, you’ll sink. But as you pick up speed, you start to float. The same principle applies to bearings.
When a bearing starts from rest, there’s no oil film, and you’re in boundary lubrication—metal rubs against metal. As the speed increases, the oil film begins to form, transitioning to mixed lubrication and eventually to full-film lubrication. However, if the speed gets too high, the rolling elements might lift off too much, causing instability—similar to a skier jumping out of the water and losing control.
This explains why:
-
Low-speed bearings or those that start and stop frequently need special lubrication considerations. They spend more time in boundary or mixed lubrication, increasing wear.
-
Oscillating bearings (those that change direction often) struggle to maintain a consistent oil film, often operating in mixed or boundary lubrication.
So, how fast does your bearing need to spin to stay “afloat”? It depends on the design, but generally, higher speeds help form a better oil film—up to a point.
Load and Lubrication: The Weight Factor
Back to our skier: imagine two skiers, one lightweight and one heavier, both moving at the same speed. The heavier skier sinks deeper into the water, getting closer to the lake bottom. Similarly, in bearings, higher loads compress the oil film, making it thinner.
If the oil film becomes too thin, you risk entering mixed or boundary lubrication, where metal surfaces can touch, increasing wear. So, for bearings under heavy loads, you might need:
-
Lubricants with higher viscosity to maintain a thicker oil film.
-
Special additives to protect against wear when the film isn’t enough.
In short, the heavier the load, the more challenging it is to keep the oil film intact. Proper lubrication becomes even more critical in these cases.
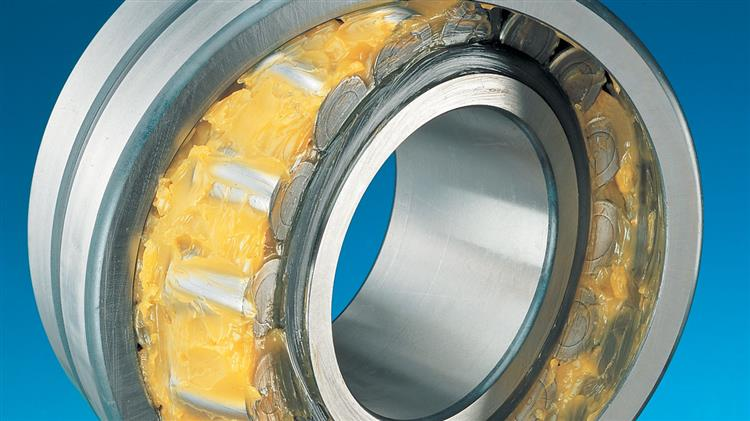
Temperature’s Role in Lubrication
Temperature and lubrication are closely linked through viscosity—the thickness of the lubricant. Generally, as temperature rises, viscosity decreases. Think of honey versus water: honey is thick and sticky, while water is thin and flows easily.
Now, imagine skiing on a lake of honey versus a lake of water. On honey, you’d float more easily because it’s thicker, but it would also be harder to move through. The same applies to bearings:
-
High-viscosity lubricants (like honey) form thicker oil films, which are great for separating surfaces but increase friction, leading to more heat generation.
-
Low-viscosity lubricants (like water) reduce friction but may not form a thick enough oil film, especially under heavy loads or low speeds.
This creates a balancing act. If the lubricant is too viscous, it generates heat, which then lowers the viscosity, potentially leading to a stable temperature. But if the balance isn’t right, you could end up with overheating or inadequate lubrication.
For engineers, this means selecting the right lubricant viscosity for the operating temperature range is crucial. Too thick, and you waste energy on friction; too thin, and you risk wear.
Conclusion: The Delicate Balance of Bearing Lubrication
Bearings and lubrication work hand in hand to keep machinery running smoothly. By understanding how speed, load, and temperature affect lubrication, you can make better decisions about lubricant selection and bearing maintenance.
To recap:
-
Speed: Higher speeds help form a better oil film, but too much speed can cause instability.
-
Load: Heavier loads thin the oil film, increasing the risk of wear.
-
Temperature: Affects viscosity, which in turn impacts the oil film and friction.
Just like a water skier needs the right speed and balance to stay afloat, your bearings need the right lubrication conditions to perform at their best. So, next time you’re working on a machine, ask yourself: is my lubrication up to speed?