Understanding Electric Motor Bearing Noise: Normal vs Abnormal Sounds
Introduction
Electric motor bearing noise has long been a concern for engineers. It is often challenging to describe the noise accurately, making it difficult for technicians to diagnose motor performance based solely on sound.
However, with years of field experience and a deep understanding of bearings, engineers can establish useful guidelines for identifying “normal” bearing noise.
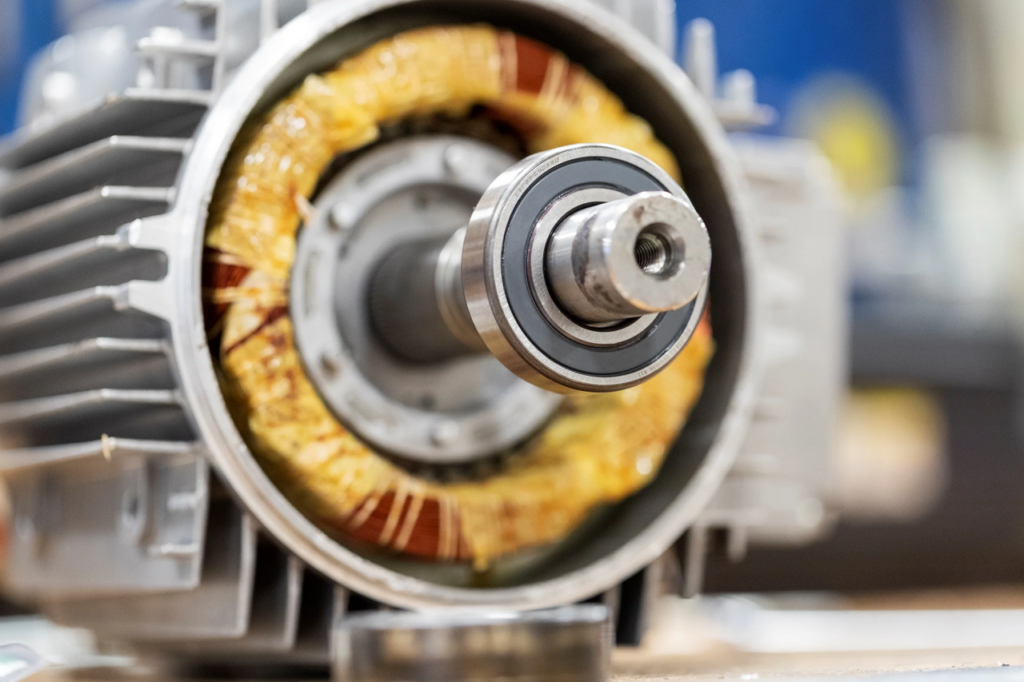
Is It Possible to Have Bearings Without Any Noise?
A common question among users is whether it’s possible to eliminate bearing noise entirely. The answer is no.
Bearings inherently produce some noise during operation. These sounds are mainly a result of the bearing’s normal function and are caused by various internal movements within the bearing. The types of noise that can be considered “normal” include:
Rolling Element and Raceway Collisions
When rolling elements run along the raceway, especially in the non-load zone, they may collide with the raceway in both radial and axial directions.
This collision occurs because the rolling elements, having left the load zone, maintain a certain speed and experience centrifugal force. This causes them to move around the shaft and collide with the raceway, producing noise. The noise is most noticeable when there is residual play in the bearing.
Rolling Element and Cage Collisions
The cage’s primary function is to guide the rolling elements. Collisions between the rolling elements and the cage, whether circumferential, radial, or axial, contribute to noise. These collisions occur in various conditions, including when rolling elements actively push the cage within the load zone or when the cage moves the rolling elements in the non-load zone.
Grease Stirring by Rolling Elements
When bearings are lubricated with grease, the rolling elements stir the grease as they move, which can generate noise.
Sliding Friction Between Rolling Elements and the Raceway
When entering the load zone, rolling elements exhibit sliding friction with raceways. Similarly, sliding friction may occur when exiting the load zone.
Other Internal Movements
Bearings with seals can also produce noise from the friction at the sealing lips.
What Is the Normal Electric Motor Bearing Noise?
As we discussed, the various internal movements in a bearing, such as collisions and friction, generate noise. For a well-maintained bearing, this noise is closely related to its speed. For example, the friction of rolling elements as they enter or exit the load zone, collisions between the rolling elements and cage, grease stirring, and friction from sealing lips all change with the bearing’s speed.
Stable and Uniform Noise
When the motor operates at a constant speed, these movements should be stable. Therefore, the noise generated by the bearing should be steady and uniform.
A normal bearing noise has two main characteristics: stability and uniformity.
However, it’s important to note that this “stability” and “uniformity” do not mean a completely unchanging sound. For instance, collisions happen repeatedly, creating a sound with a small periodic cycle. At the same time, continuous noises, such as friction from sealing lips, may also be present.
In actual working conditions, certain interferences can cause noise, but it should still maintain a stable and uniform pattern. In such cases, the noise may not match the bearing’s expected frequency, indicating an issue. Therefore, when diagnosing bearing noise on-site, it is crucial to look for stability and uniformity, as well as a lack of abnormal frequencies.
Abnormal Bearing Noise: What to Look Out For
Electric motor bearing noise can also signal potential failures or defects in the bearing or associated components.
This type of noise is different from normal bearing noise and is referred to as “abnormal noise.”
Abnormal bearing noise is typically caused by defects within the motor or bearing, leading to extra vibrations and noise. These sounds are the external manifestation of internal faults.
Causes of Abnormal Noise
-
Internal Bearing Defects: If there are any defects, such as cracks or wear, they can lead to abnormal vibrations and, consequently, noise. These faults are important to identify and eliminate.
-
Other Mechanical Failures: Sometimes, faults in other motor components, such as the shaft or housing, can result in abnormal noise that is perceived as bearing-related.
Abnormal noise should be investigated and fixed, as it indicates a failure or potential failure within the motor system. Fortunately, this type of noise is generally reversible once the underlying issue is addressed.
Challenges in Diagnosing Bearing Noise
Diagnosing bearing noise involves considering a variety of factors, especially in real-world conditions. One of the challenges is that noise is essentially a vibration transmitted through the air to the ear. This process can be influenced by the environment and the hearing sensitivity of the person conducting the diagnosis.
Environmental Interference
Electric motors produce various noises beyond just bearing noise, such as fan noise, electromagnetic noise, and mechanical noise from other components. These noises can mix with bearing noise, making it difficult for technicians to isolate the bearing’s noise from other sources.
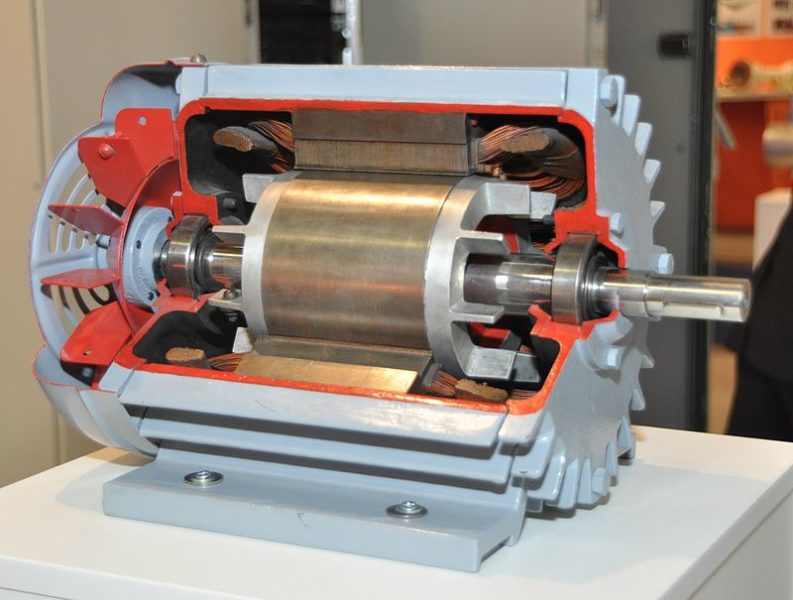
Sensitivity of Hearing and Equipment
Human hearing can be subjective, and environmental noise can affect the accuracy of both manual and electronic measurements. Special conditions are required for noise testing to ensure accurate results, and in many cases, on-site diagnosis relies more on qualitative methods than quantitative analysis.
Methods for Bearing Noise Diagnosis
Despite the challenges, it’s possible to diagnose bearing noise using advanced tools and techniques. The methods for noise analysis are similar to vibration analysis, including both time-domain and frequency-domain analysis.
Time-Domain Analysis
This approach involves examining the noise over time to identify patterns or fluctuations in the sound, which may indicate an abnormal condition.
Frequency-Domain Analysis
This method helps isolate different frequencies in the noise, allowing engineers to identify specific faults related to the bearing.
In ideal testing conditions, frequency-domain analysis can help separate bearing noise from other types of noise, such as electromagnetic or fan-related sounds, and help pinpoint any specific faults within the bearing.
On-Site Applications of Bearing Noise Analysis
In practical situations, it’s difficult to achieve the ideal testing conditions required for a comprehensive analysis.
Therefore, most on-site noise analysis is qualitative rather than quantitative. This involves listening to the noise produced by the bearing and comparing it to known normal or abnormal sound patterns.
Qualitative Noise Analysis
Experienced engineers rely on their auditory skills to diagnose the noise, often comparing the noise to stored samples of typical bearing sounds. However, human hearing can vary, so noise analysis is typically used as a complementary tool for fault diagnosis, rather than a standalone method.
Conclusion
In conclusion, while electric motor bearing noise is inevitable, understanding what constitutes normal versus abnormal noise is crucial for effective diagnosis.
Normal noise is stable and uniform, linked to bearing function, whereas abnormal noise often signals internal defects or mechanical issues.
Regular monitoring and noise analysis can help identify potential problems early, ensuring smoother motor operation and preventing costly failures.
If you have any questions about motor bearings, feel free to contact TFL Bearings. We provide high-quality bearings and professional consulting services.