Understanding Roller Bearing Heat Generation: Causes and Solutions
Introduction
Roller bearings are essential components in modern mechanical systems, ensuring the smooth operation of rotating parts.
However, roller bearing heat generation is a frequent problem that can seriously affect equipment longevity and performance.
Understanding the mechanisms behind heat generation in bearings is necessary for effective maintenance and design optimization.
In this article, we’ll explore the science behind roller bearing heat generation, identify when it becomes abnormal, and provide practical solutions for managing excessive heat.
The Physics Behind Roller Bearing Heat Generation
Roller bearings operate under various physical principles that lead to heat generation.
The primary source of heat is friction, which occurs between the rolling elements and the inner and outer races. This friction results in energy loss, which is converted into heat, increasing the bearing’s temperature.
While some heat generation is normal, excessive heat can be problematic, leading to reduced performance and potential damage.
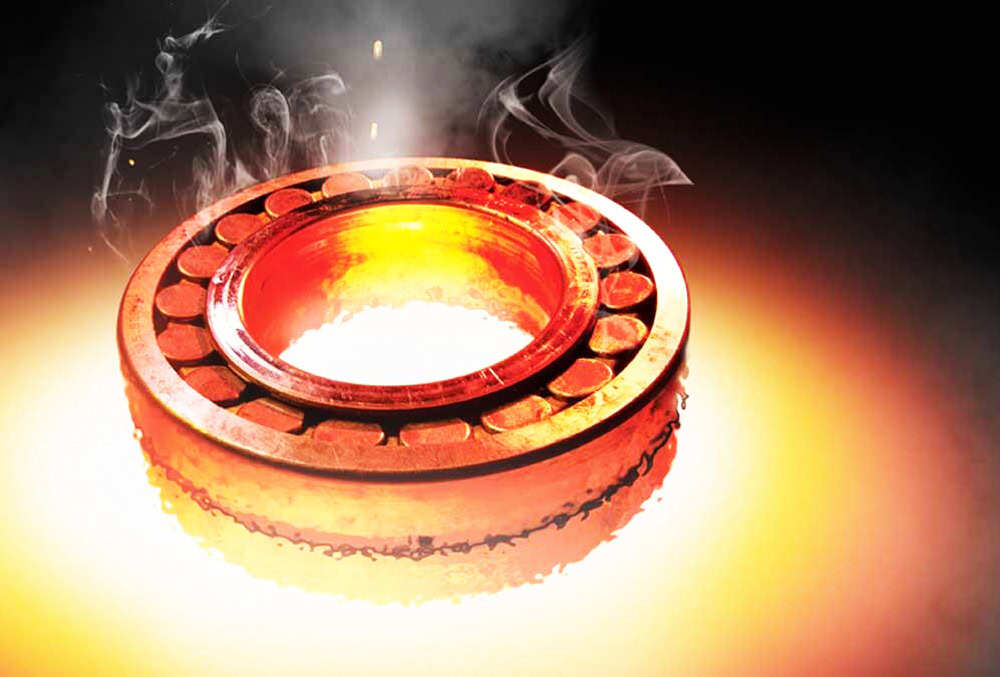
Rolling and Sliding Friction: The Primary Heat Source
The heat generated in a roller bearing primarily stems from the friction between the rolling elements and the raceways.
As the rolling elements move along the raceways, friction inevitably occurs. Rolling friction typically causes less energy loss than sliding friction, but under high-speed or heavy-load conditions, the energy loss increases, generating significant amounts of heat.
Additionally, microscopic surface irregularities cause rolling elements and raceways to involve some sliding friction instead of pure rolling contact. This sliding generates heat through energy loss, becoming a major heat source in roller bearings.
The Fiction of the Cage: Effects of Structure and Material
The bearing cage is another critical factor in heat generation. Its role is to evenly space the rolling elements and prevent them from making direct contact with each other.
However, friction between the cage and the rolling elements can generate heat. If the cage material or design is below average or if the manufacturing quality is poor, friction increases, leading to more heat.
Furthermore, the cage’s movement during operation also causes resistance, contributing further to energy loss and heat generation.
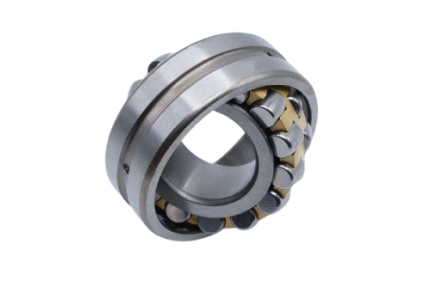
Lubricating Oil Shear Friction: Lubrication and Heat Generation
Lubricants play a dual role in bearings: they reduce friction and help dissipate heat.
As the lubricant flows within the bearing, it experiences shear forces. The greater the viscosity of the lubricating oil, the greater the shear friction. When the bearing runs at high speed, the shear friction of the lubricating oil will generate a large amount of heat.
If the lubricating oil is insufficient or the grease deteriorates, dry friction or semi-dry friction may occur between the rolling elements and the inner and outer rings. The energy loss of this kind of friction is very large, which will cause the bearing to heat up rapidly.
Elastic Deformation: The Transformation Process of Stress and Energy
When the rolling elements come into contact with the inner and outer rings, relatively large contact stress will be generated. This stress causes elastic deformation on the contact surface.
During the rolling process, repeated changes in elastic deformation consume energy, which is then converted into heat. If the bearing’s manufacturing precision is low or the installation is improper, it may lead to local stress concentration.
In areas with local stress concentration, the elastic deformation is more significant, and the energy loss is greater, thus generating more heat.
Vibration and Impact: Additional Heat Sources under Dynamic Loads
During operation, the bearing may be affected by external vibrations or internal unbalanced forces, resulting in vibration.
Vibration causes continuous changes in the contact state between the rolling elements and the inner and outer rings, increasing friction and energy loss.
In addition, when the bearing is subjected to impact loads, the contact stress between the rolling elements and the inner and outer rings increases instantaneously, leading to intensified local elastic deformation and friction. The impact of friction generates a large amount of heat.
When is Heat Generation Abnormal?
While some heat generation in roller bearings is expected, excessive or abnormal heating can signal underlying issues. If not addressed promptly, abnormal heat generation can lead to reduced bearing performance and even failure.
Signs of Abnormal Heat Generation
There are several indicators that the heat generation in a bearing may be abnormal:
-
Temperature Increase: If the bearing’s temperature rises significantly above the surrounding components, it could be a sign of excessive friction or poor lubrication.
-
Inconsistent Temperature Trends: If the temperature change trend of the bearing differs from the surrounding components, it may indicate a problem.
-
Noise and Vibration: Abnormal noise or vibration may accompany excessive heat generation. These could be caused by internal wear, poor lubrication, or misalignment of the bearing.
-
Lubricant Degradation: Lubricant deterioration or leakage may also be linked to abnormal heating. High temperatures accelerate lubricant degradation, reducing lubricity and intensifying frictional heating in a vicious cycle.
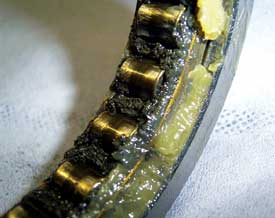
The Impact of Abnormal Heat
When heat generation exceeds normal levels, it can lead to a range of issues:
-
Bearing Wear and Damage: High temperatures can cause excessive wear, leading to bearing failure.
-
Lubricant Breakdown: Excessive heat accelerates the degradation of the lubricant, further increasing friction.
-
Structural Changes: Prolonged exposure to high temperatures can lead to changes in the internal structure of the bearing, affecting its performance and longevity.
How to Handle Abnormal Heat in Roller Bearings
If abnormal heat generation is detected, immediate action is required to prevent long-term damage to the bearing and surrounding equipment. Several strategies can help reduce and manage bearing temperature.
Check Lubricant Condition
Lubricants are critical in reducing friction and dissipating heat. Ensure that the lubricant is adequate, fresh, and not contaminated.
If the lubricant is insufficient or degraded, replace it with the correct type and viscosity that matches the operating conditions. Proper lubrication ensures smooth operation and helps regulate the bearing temperature.
Inspect Bearing Installation
Correct installation is crucial to the bearing’s performance. Misalignment, eccentricity, or loose installation can increase friction, causing abnormal heat generation.
Regularly check the installation to ensure that the bearing is aligned correctly and is secure. Proper installation minimizes unnecessary friction and ensures the bearing operates efficiently.
Monitor Load Conditions
Excessive loads can increase the stress on the bearing and lead to higher friction and heat generation.
If the bearing is subjected to excessive load, consider adjusting the equipment’s operating parameters to reduce the load.
In some cases, modifying or upgrading the equipment may be necessary to accommodate larger loads.
Take Preventative Measures
If abnormal heat persists despite these actions, it may be necessary to consult with professional maintenance personnel or the bearing manufacturer for further inspection.
Specialized tools can help identify the root causes of the heat generation and suggest more targeted solutions.
Conclusion
Roller bearing heat generation is a natural process, but when it becomes excessive, it can lead to serious issues that affect bearing performance and equipment reliability.
By understanding the causes of bearing heat and implementing appropriate solutions, it’s possible to mitigate the risks associated with abnormal heat.
Regular maintenance—such as checking lubricant condition, ensuring proper installation, and monitoring load conditions—can prevent many of the issues that lead to excessive heat generation.
In the long run, understanding the mechanisms behind bearing heat and addressing abnormal heat generation promptly can significantly extend the life of roller bearings and enhance the overall performance of mechanical systems.
Troubled by bearing overheating? TFL Bearings offers high-quality bearings and systematic solutions. Contact us anytime!