Precision Bearing Solutions for Extreme Working Conditions: Helping Fujian Sansteel Improve Production Efficiency
Abstract
The stable operation of rolling mill gear reducers is a critical prerequisite for ensuring smooth rolling production. This paper combines theoretical and practical approaches to investigate the causes of bearing failure in the high-speed shafts of horizontal gear reducers in bar mills. The analysis focuses on both equipment and process factors to understand the failure mechanism and proposes effective solutions for improvement. Two replacement strategies for the high-speed shaft bearings were developed: substituting SKF23230CC/W33 bearings with NSK23230CAME4S11 bearings or FAG F-674572.23130 bearings. Results demonstrate that these replacements effectively eliminated operational risks, reduced equipment failure rates, and provided valuable insights for addressing similar issues in the metallurgical industry.
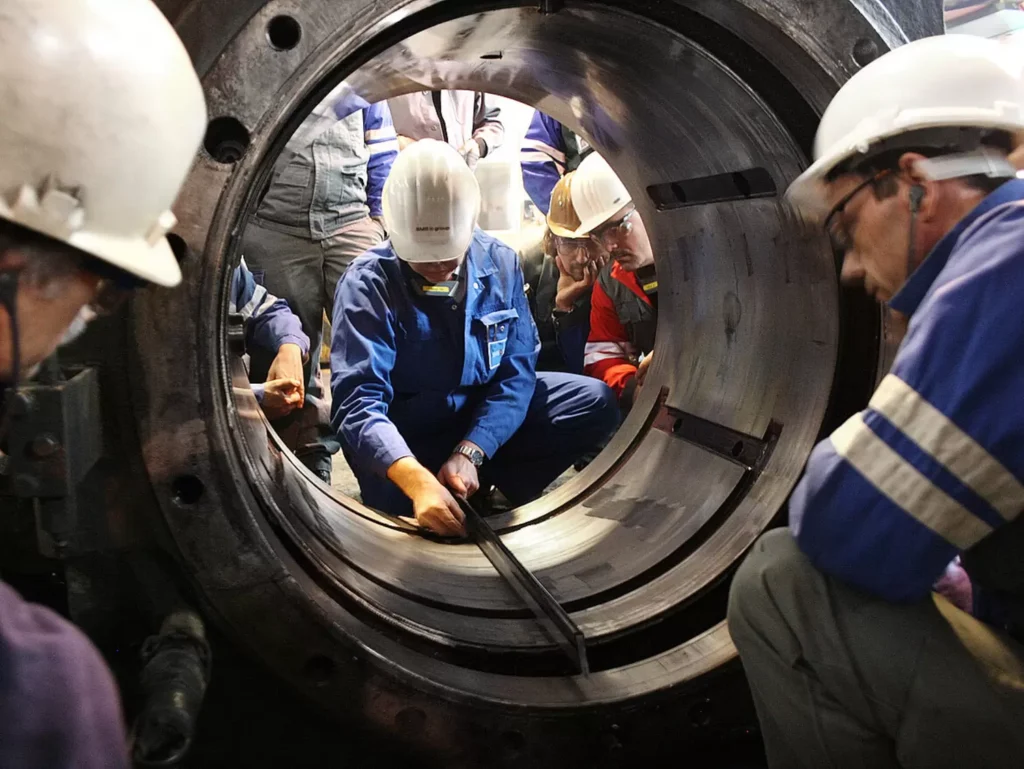
Keywords: Gear Reducer; High-Speed Shaft; Bearing Failure
1. Introduction
Our customer, Fujian Sansteel, is a modern steel producer whose bar production line undertakes high-intensity, high-precision rolling tasks. With the upgrading of the production line in 2020, the line is facing serious equipment challenges: frequent bearing damage seriously affects production continuity and economic efficiency.
Rolling mill gear reducers are primarily used in production lines for bars, wires, and profiles. Their main function is to transmit motion and torque from the motor to the rolls, meeting the torque and speed requirements of the mill. As one of the most critical components in rolling production lines, a gear reducer failure can lead to production downtime and significant impacts on operations. Given their harsh operating conditions, it is crucial to carefully select bearings that meet the demands of the application during the design process. This study analyzes bearing failures in high-speed shafts of horizontal gear reducers in the mid-roll section of Fujian Sangang’s bar mill. By addressing these failures and optimizing the high-speed shaft components, we aim to resolve equipment risks and provide reference solutions for the metallurgical industry.
2. Problems Identified
The bar mill at Fujian Sangang primarily produces rebar in sizes ranging from Φ18mm to Φ40mm. In August 2020, to reduce production costs and minimize alloy consumption, the production line was upgraded from a split-type line to a composite line capable of producing both standard and high-strength rebars.
After the upgrade was completed in December 2020, bearing failures began to occur on the positioning end of the high-speed shaft in the horizontal gear reducers of the mid-roll section. Starting in June 2021, incidents of bearing cage fractures and dislodgement were reported, leading to severe rolling interruptions. Table 1 illustrates the bearing failure conditions observed in the mid-roll section.
3. Cause Analysis
Following the upgrade, the layout of the process plane between the 6# rolling mill and the 2# flying shear is shown in Figure 1. The mid-roll section (7#–12# rolling mills) alternates between horizontal and vertical layouts. Rolling mills 7#–10# are of the open-type design, while 11# and 12# are closed-type. When producing larger diameters (Φ28mm, Φ36mm, and Φ40mm), rolling mills 9# and 10# are bypassed.
To streamline spare part inventories and reduce costs, the design of horizontal gear reducers in rolling mills 7#, 9#, and 11# ensured compatibility in components, except for differences in gear ratios. The internal structure of the horizontal gear reducer is shown in Figure 2, with the high-speed shaft supported by two SKF23230CC/W33 spherical roller bearings.
The operating characteristics of rolling mill gear reducers include low speed, heavy load, high impact frequency, and the need for continuous operation. Lubrication checks confirmed that the oil pressure and flow rate met design requirements. As shown in Figure 2, the high-speed shaft rotates counterclockwise with a right-hand helical gear, directing axial forces toward the floating-end bearing. Cage fractures occurred at the junction of the outer ring supports, which failed to withstand the axial displacement and impact.
4. TFL BEARINGS Customized Solutions
Frequent bearing failures in the horizontal gear reducers of the mid-roll section disrupted production and necessitated urgent optimization. Two improvement strategies were proposed:
1. **Brand Replacement**: Bearing cage fractures were attributed to high impact loads and significant axial displacement. During operation, the bearing’s inner ring and rollers decelerate momentarily upon steel entry, while the cage maintains its original speed due to inertia. This causes instantaneous collisions, leading to cage failure. Copper cages, while less resistant to speed, offer superior load capacity. Based on performance requirements, NSK23230CAME4S11 bearings with copper cages were selected.
2. **Model Replacement**: FAG’s F-674572.23130 bearings feature thicker, high-strength copper cages. These bearings were identified as suitable replacements for the high-speed shaft components, as shown in Figure 3.
5. Implementation Results
The solutions were implemented at different times and levels of complexity across the 7#, 9#, and 11# reducers:
1. **7# Reducer**: After replacing the SKF23230CC/W33 bearing in July 2021, failures occurred again by August 2022. Subsequently, the high-speed shaft components were pre-assembled with FAG bearings and installed during the next failure. Since August 2022, no further issues have been reported.
2. **9# Reducer**: In January 2023, SKF bearings were replaced with NSK23230CAME4S11 bearings. Since then, the reducer has operated without failures.
3. **11# Reducer**: Following a second failure in September 2021, the NSK23230CAME4S11 bearings were installed. The reducer has experienced no further issues.
6. Conclusion
After upgrading the bar mill to a composite production line, the mid-roll section gear reducers experienced frequent bearing failures. By analyzing the root causes from design and operational perspectives, two effective solutions were implemented:
1. Replacing SKF23230CC/W33 bearings with NSK23230CAME4S11 bearings resolved operational risks.
2. Replacing SKF23230CC/W33 bearings with FAG F-674572.23130 bearings eliminated recurring failures.
These measures effectively addressed equipment risks, providing valuable experience for the metallurgical industry.
7. Effectiveness and Value of Implementation
- Significantly extended bearing life
- Reduced gearbox operational stability by more than 85
- Reduced annual equipment maintenance costs by approximately 40
8. Customer Benefits
- Significant increase in production continuity
- Significant reduction in equipment failure rate
- Significant reduction in maintenance costs
- Overall optimization of production efficiency
9. Technical Innovation Highlights
- Bearing design that accurately matches the characteristics of working conditions
- Synergistic optimization of material and structure
- Deep understanding of customers’ production process pain points
10. Industry applicability
The solution is not only applicable to bar rolling, but also to a wide range of applications:
- Wire rod production lines
- Rolling facilities for steel sections
- Metallurgical heavy-duty equipment
- Continuous production equipment
11. Why TFL BEARINGS
- Customized Solutions
- In-depth technical support
- Continuous performance optimization services
- Comprehensive engineering consulting