The Inspection and Adjustment of Work Roll Bearings in Four-High Rolling Mills
Introduction
In the world of rolling mills, work roll bearings play a critical role in ensuring smooth and efficient production. These bearings support the rolls, maintain their correct position within the frame, and reduce friction and wear between the rolls and their supports.
As rolling speeds increase and tolerance requirements tighten, the importance of proper maintenance, inspection, and adjustment of these bearings becomes even more crucial. This article delves into the significance of work roll bearings in four-high rolling mills, their working conditions, structure, and the essential steps for their inspection and adjustment.
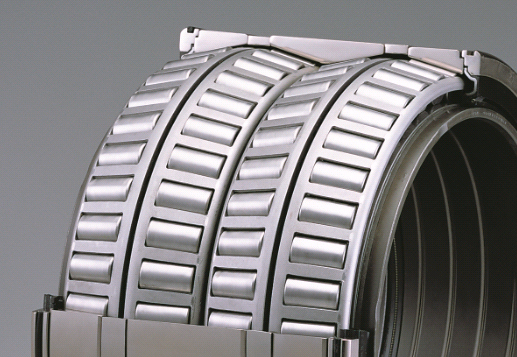
The Role of Work Roll Bearings in Rolling Mills
Work roll bearings are indispensable in rolling mills. They serve several key functions:
-
Support and Positioning: Bearings provide stable support for the rolls, ensuring they remain correctly positioned within the mill frame. This reduces unnecessary movement and vibration during operation, allowing the rolls to rotate or move smoothly.
-
Load Bearing: They withstand various loads generated during rolling, such as radial, axial, and bending forces. By evenly distributing these loads, bearings protect the rolls and other components, enhancing their lifespan and reliability.
-
Precision and Guidance: With precise design and dimensions, bearings ensure the rolls maintain their intended position and angle, contributing to the mill’s overall stability and accuracy.
-
Vibration and Noise Reduction: Bearings absorb vibrations and shocks, minimizing noise and protecting the mill from damage.
-
Adjustment and Control: When rolls wear or deform, bearings can be adjusted to restore the mill’s performance, extending its operational life.
-
Sealing and Protection: Some bearings feature seals that prevent dust, water, and debris from entering, ensuring clean lubrication and prolonging bearing life.
In short, work roll bearings are the backbone of a rolling mill’s efficiency and longevity. But what happens when they aren’t properly maintained?
Working Conditions of Work Roll Bearings in Four-High Rolling Mills
The environment in a four-high rolling mill is harsh. High temperatures, dust, and cooling water create a challenging setting for bearings.
In the case of a second-hand four-high reversible rolling mill from Spain, originally produced by the American company Mesta in the 1940s, these conditions are particularly demanding. Dust and cooling water can easily infiltrate the bearing housing, leading to lubrication failure and surface damage.
Between May and June 2012, a series of bearing failures occurred at a plate manufacturing company, resulting in significant economic losses. Four incidents of bearing burnout and seizure cost over 1 million yuan, with each bearing set priced at over 300,000 yuan and requiring an 18-month processing cycle. These failures weren’t due to poor bearing quality but rather improper assembly, inspection, and adjustment.
This highlights the critical need for correct maintenance practices to extend bearing life.
Structure of Work Roll Bearings
The work roll bearings in the rolling mill are four-row tapered roller bearings produced by TIMKEN, model EE749259DW-749335-749335CD. Key specifications include:
-
Inner diameter: 660.01 mm
-
Outer diameter: 855.014 mm
-
Total width: 320 mm
-
Radial load capacity: 1,314 kN
-
Axial load capacity: 226.8 kN
-
Rated speed: 500 r/min
The bearing consists of two double inner rings, one double outer ring, two single outer rings, two outer adjusting spacers, one inner adjusting spacer, rolling elements, and cages. Its design offers high rotational accuracy, low friction, and separable inner and outer rings, making inspection and adjustment straightforward.
Inspection and Adjustment of Work Roll Bearings
Proper inspection and adjustment are vital to maintaining bearing performance. This process can be divided into three main categories:
Inspection During Operation
Regular checks are essential to ensure bearings function correctly. According to process regulations, bearings should be inspected by:
-
Listening: Use a specialized tool to detect any impact or mechanical friction sounds from the bearing.
-
Observing: Check the installation position and lubrication status.
-
Measuring: Monitor vibration and offset to determine if the bearing is operating normally.
If any abnormalities are detected, immediate action should be taken. Have you ever wondered how a simple sound check could save thousands in repair costs?
Inspection in a Stationary State
When the mill is not in operation, inspect the fastening of related components to ensure they are in the correct position. Excessive axial movement of the roll can lead to increased axial forces and severe impacts on the bearing. Regular checks of component tightness can reduce damage to the bearing and extend its lifespan.
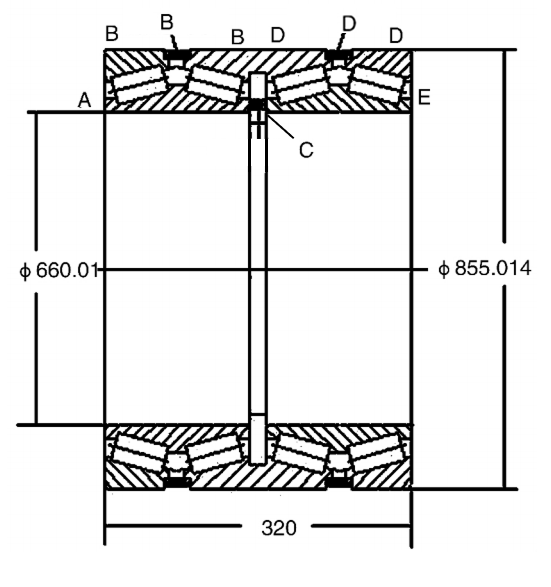
Disassembly and Inspection
Bearings must be periodically removed from the housing for thorough inspection. The frequency depends on production volume, typically every three months, six months, or annually. During inspection:
-
Record Bearing Position: Note the bearing’s installation position, time in service, and the previously used load zone on the outer ring.
-
Remove the Bearing: Use specialized tools to carefully lift the bearing from the housing.
-
Clean the Bearing: Use kerosene or a dedicated cleaner to remove debris and assess wear.
-
Visual Inspection: Check for wear on the rolling elements, inner ring raceways, and outer ring. Minor peeling can be smoothed, but if damage exceeds 1/4 of the raceway width, the bearing should not be repaired.
-
Measure and Adjust Clearance: Place the bearing on a platform and measure the clearance at four points using a feeler gauge. Adjust the spacers to maintain the required clearance, typically 1.5 times the original value.
-
Inspect the Bearing Housing: Clean and check the lubrication channels, ensuring the housing’s dimensions and cylindricity meet assembly requirements.
-
Check Seals: Inspect seals for wear or damage and replace if necessary.
-
Reassemble the Bearing: Apply lubrication to the housing, reassemble the bearing in the correct order, and rotate the load zone to a new position to extend bearing life.
Results of Proper Inspection and Adjustment
After implementing these inspection and adjustment practices, the rolling mill’s work roll bearings performed reliably for over six months without any incidents. This not only ensured the bearings’ expected lifespan but also reduced unnecessary adjustments, saving manpower and resources while maintaining smooth production.
Conclusion
Many factors influence bearing lifespan, including tolerance fits, clearance selection, seal quality, and lubricant choice. Additionally, the magnitude and fluctuation of rolling forces play a significant role.
While bearing wear can take various forms, understanding the causes of damage and implementing proper maintenance, inspection, and adjustment can prevent failures. By maximizing bearing efficiency and minimizing consumption, mills can achieve cost savings and improved operational reliability.
Are you ready to optimize your rolling mill’s performance? Start by prioritizing bearing inspection and adjustment today!