Electrically Insulated Bearings: Which Method Is Best for You?
Introduction
Electrically insulated bearings are essential in preventing electrical damage in various industrial applications, such as motors, generators, and other equipment exposed to electrical currents. These bearings protect against premature wear, reduce maintenance costs, and extend the lifespan of machinery.
But with several methods available to achieve electrical insulation, how do you choose the right one? In previous articles, we covered how to select materials for bearings. In this article, we’ll explore the four main ways to implement electrical insulation in bearings—ceramic coatings, special PPS coatings, hybrid ceramic bearings, and insulated bearing sleeve structures—and help you decide which might be the best fit for your needs.
What Are Electrically Insulated Bearings?
Before diving into the methods, let’s quickly understand why electrical insulation in bearings is so important. In environments where bearings are exposed to electrical currents—such as in electric motors or generators—these currents can pass through the bearing, causing electrical erosion.
This leads to pitting, fluting, and eventually, bearing failure. Electrically insulated bearings prevent this by creating a barrier that stops the current from passing through the bearing, ensuring longer life and smoother operation.
Now, let’s explore the four key methods used to achieve this insulation.
Ceramic Coatings: A Durable and Reliable Choice
Ceramic coatings are one of the most popular methods for electrically insulating bearings. By applying a thin layer of ceramic material to the bearing’s surface, this method provides excellent protection against electrical currents.
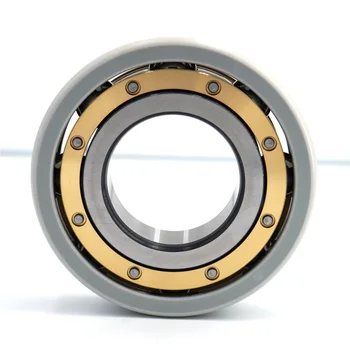
-
Material Selection: Ceramic coatings typically use high-hardness, wear-resistant materials like aluminum oxide (Al₂O₃), which also offer good thermal conductivity.
-
Coating Process: Advanced techniques like plasma spraying are used to evenly apply the ceramic layer to the bearing’s outer or inner ring. The coating is usually between 0.2mm and 0.4mm thick, ensuring sufficient insulation strength and durability.
Performance Benefits
-
Superior Insulation: Ceramic coatings significantly enhance the bearing’s electrical insulation, preventing current from passing through and causing damage.
-
Chemical Stability: The coating is chemically stable and resistant to aging, ensuring long-term reliability.
-
Wear Resistance: Ceramic materials are highly durable, which helps extend the bearing’s lifespan even in demanding environments.
Drawbacks
-
Adhesion Requirements: The coating must adhere strongly to the bearing’s surface, which can be challenging and requires precise application.
Is ceramic coating the right choice for you? If you need a balance of durability, insulation, and long-term performance, this method is worth considering.
Special PPS Coatings: High-Performance Polymer Insulation
Another effective way to insulate bearings is through special PPS (Polyphenylene Sulfide) coatings. PPS is a high-performance polymer known for its excellent insulation properties, and special formulations take this a step further.
How It Works
-
Material Properties: PPS is a polymer with outstanding insulation capabilities. Special PPS coatings are enhanced to provide even higher insulation resistance and breakdown voltage.
-
Coating Application: The coating is applied to the bearing’s outer or inner ring, forming a dense, protective insulation layer.
Performance Benefits
-
Excellent Insulation: Special PPS coatings offer superior electrical insulation, even in harsh environments.
-
Chemical Stability: Like ceramic coatings, PPS is chemically stable and maintains its properties over time.
-
Cost-Effective: The coating process is relatively simple and scalable, making it an economical choice for many applications.
Drawbacks
-
Wear Resistance: While PPS coatings are durable, they may not match the wear resistance of ceramic coatings, so regular maintenance might be needed.
Is special PPS coating the way to go? If you’re looking for a cost-effective solution with strong insulation properties, especially in less abrasive environments, this could be your answer.
Hybrid Ceramic Bearings: Combining Strength and Insulation
Hybrid ceramic bearings (e.g. 608 skate bearing hybrid ceramic ball bearing) offer a unique approach to electrical insulation by using ceramic rolling elements (such as silicon nitride) paired with steel inner and outer rings. This design not only provides excellent insulation but also enhances the bearing’s overall performance.
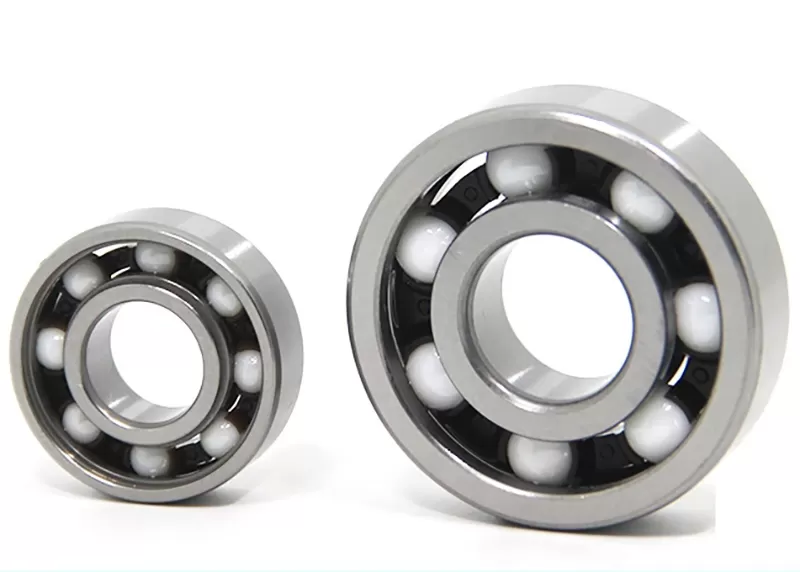
How It Works
-
Structure: The rolling elements (balls or rollers) are made from ceramic, while the rings are made from bearing steel.
-
Insulation Principle: Ceramic has a much higher electrical resistance than steel, so current cannot easily pass through the rolling elements, effectively insulating the bearing.
Performance Benefits
-
High Strength and Durability: The steel rings provide strength, while the ceramic rolling elements offer wear resistance and insulation.
-
Suitable for Harsh Conditions: Hybrid ceramic bearings excel in high-speed, high-temperature, and high-humidity environments.
-
Low Friction: Ceramic rolling elements have a lower friction coefficient, allowing for higher speeds and smoother operation.
Drawbacks
-
Higher Cost: The manufacturing process for ceramic rolling elements is complex and costly, making these bearings more expensive.
-
Precision Requirements: Producing ceramic rolling elements requires high-precision equipment and expertise.
Are hybrid ceramic bearings worth the investment? If you need top-tier performance in extreme conditions and can accommodate the higher cost, this method is hard to beat.
Insulated Bearing Sleeve Structures: Simple and Effective
Sometimes, the simplest solutions are the most effective. Insulated bearing sleeve structures add an extra layer of insulation material to the bearing, creating a barrier against electrical currents.
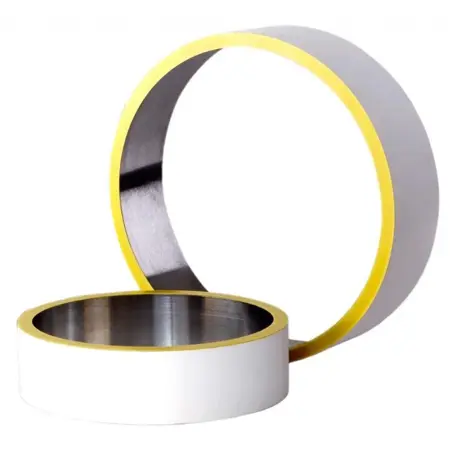
How It Works
-
Design: An insulation layer is added to the bearing’s outer or inner sleeve, forming an electrical barrier.
-
Insulation Principle: The insulation material prevents current from passing through the sleeve to the bearing, protecting it from electrical damage.
Performance Benefits
-
Simplicity: This method is straightforward to implement and easy to maintain.
-
Customizable: Different insulation materials can be used to meet specific requirements.
-
Cost-Effective: Generally, this is one of the more affordable options for achieving electrical insulation.
Drawbacks
-
Variable Performance: The effectiveness of the insulation can depend on the material chosen, the manufacturing process, and the installation quality.
-
Stability in Extreme Conditions: In very harsh environments, this method may not be as reliable as others, such as ceramic coatings or hybrid bearings.
Is an insulated bearing sleeve structure the best fit? If you’re looking for a budget-friendly, easy-to-install solution for less demanding applications, this could be the way to go.
Which Method Is Best?
So, which of these methods is the best for electrically insulated bearings? The answer depends on your specific needs, including the application environment, performance requirements, and budget. Let’s summarize the key considerations:
-
Ceramic Coatings: Ideal for applications requiring high durability, excellent insulation, and long-term reliability. Best for demanding environments where wear resistance is crucial.
-
Special PPS Coatings: A cost-effective option with strong insulation properties, suitable for less abrasive conditions where budget is a concern.
-
Hybrid Ceramic Bearings: Perfect for high-speed, high-temperature, or high-humidity environments where top performance is needed, but comes at a higher cost.
-
Insulated Bearing Sleeve Structures: Simple, affordable, and easy to maintain, making them a great choice for less extreme conditions.
Still unsure? Consider consulting with a bearing expert to evaluate your specific requirements and find the optimal solution.