Cylindrical Roller Bearings: Top 5 Advantages | TFL Bearings
Introduction
High Load-Bearing Capacity Of Cylindrical Roller Bearings
Line contact design of cylindrical roller bearings
One of the main structural features of cylindrical roller bearings is the use of cylindrical rollers to achieve line contact. The design feature of line contact is that it can disperse stress to multiple contact points. Compared with spherical rolling elements, cylindrical rollers have a longer contact surface, which makes the load distribution per unit contact area more uniform so that they can withstand larger loads. Due to the geometry and arrangement of the cylindrical rollers, the bearings can evenly share the load during operation, reducing local load concentration and wear and thereby improving the load-bearing capacity.
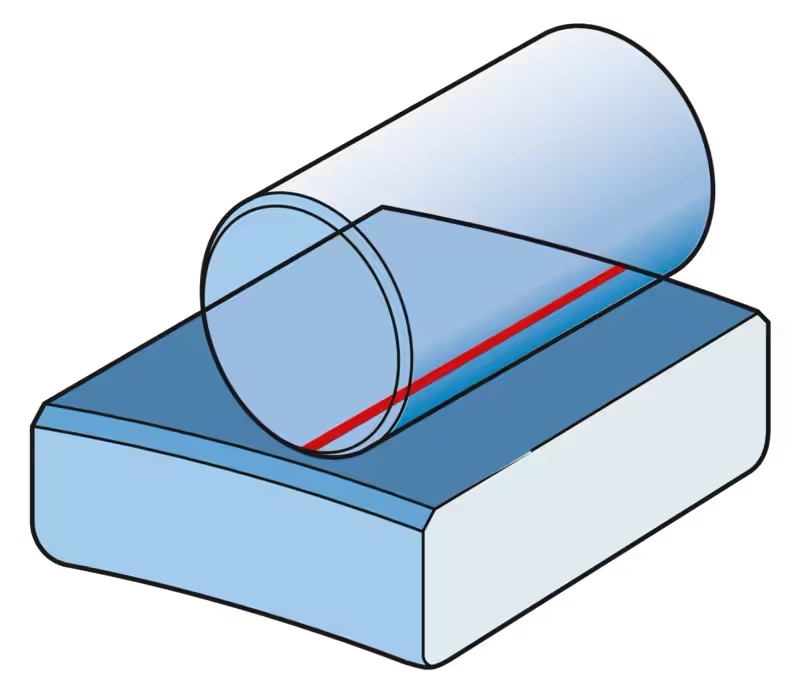
Multi-row roller structure of cylindrical roller bearings
In addition, increasing the number of roller rows can make the load distribution more uniform. For example, in double-row cylindrical roller bearings or multi-row cylindrical roller bearings, each row of rollers bears less load, which helps reduce local stress concentration and the risk of damage to individual rollers. More rows can also increase the number of rollers, further improving the overall load capacity and life.
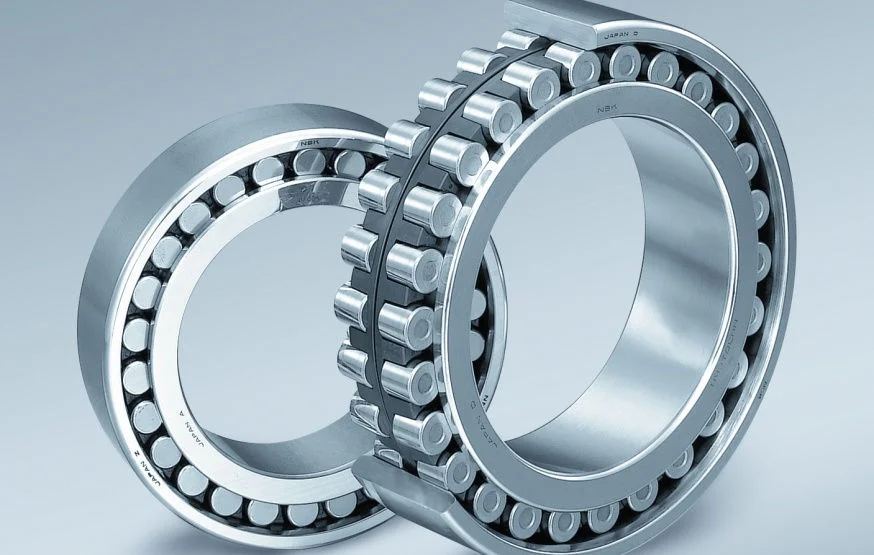
High Radial Clearance Of Cylindrical Roller Bearings
What is radial clearance
Tolerance for Shaft Misalignment
The wide radial clearance of cylindrical roller bearings can accommodate slight shaft misalignment and reduce stress during operation. This improves the fault tolerance of the bearing for equipment that requires high-precision positioning. Therefore, cylindrical roller bearings are suitable for some application environments that do not require high shaft alignment.
Shock Absorption in Dynamic Environments
In some dynamic application scenarios, such as construction machinery and railway vehicles, the equipment may encounter severe vibration and shock loads, which may cause damage to the bearing. The design with the wide radial space can effectively handle vibration and absorb shock forces. This keeps the equipment more stable overall and reduces the damage caused by strong shocks.
Enhanced flexibility for thermal expansion
The high radial clearance design allows free expansion under high-temperature or temperature-difference conditions without affecting bearing performance. Loose radial clearance can better accommodate misalignment between the shaft and the bearing seat, thereby offsetting the interference fit. This supports the bearing to offset the expansion or contraction of the shaft or the bearing seat caused by temperature changes. Therefore, cylindrical roller bearings can maintain stable operation in some harsh environments.
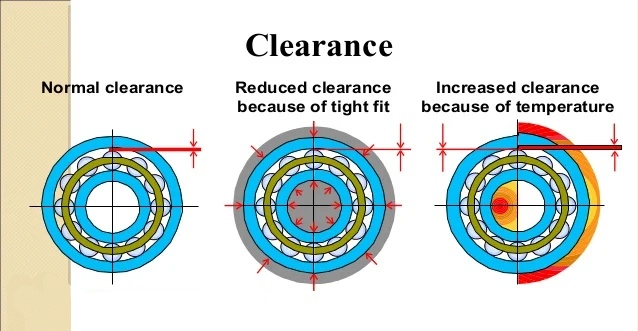
Contamination Resistance Of Cylindrical Roller Bearings
When it comes to industrial and automotive applications, contamination resistance is a critical feature for cylindrical roller bearings. Dust, debris, and other contaminants can quickly damage components and reduce performance. Bearings like N, NJ, NU, and NUP series are designed to withstand these challenges, ensuring durability and reliability even in harsh environments. Let’s break down how each type performs in contamination resistance:
Type | Features Enhancing Contamination Resistance | Best Suited Applications |
---|---|---|
N Series | Simplified design with separable inner and outer rings allows for easier cleaning and maintenance, minimizing the impact of debris. | Applications with periodic maintenance schedules, such as general industrial machinery. |
NJ Series | Can handle both radial loads and axial loads in one direction, with tight tolerances to reduce entry points for contaminants. | Gearboxes and transmissions where axial and radial load coexist with exposure to particulate contaminants. |
NU Series | Designed for high-speed operations with minimized friction; excellent lubricant retention to combat contamination effects. | High-speed machinery like compressors and turbines that operate in moderately clean environments. |
NUP Series | Similar to NJ but supports axial loads in both directions, often with end-cap seals for added protection against contamination. | Automotive components and industrial systems requiring dual axial load management and higher resistance to external pollutants. |
Easy Mounting and Maintenance Of Cylindrical Roller Bearings
Easy Replacement of Components
Cylindrical roller bearings are designed to be simple and separable, making them easy to install, remove, and replace. This reduces the need for specialized skills and tools for installation or maintenance. The simple structure significantly reduces the cost of bearings over the entire life cycle of the equipment while improving operational efficiency. Maintenance personnel can complete the installation of new components in a shorter time. This reduces the labor cost required for installation and reduces machine downtime, bringing greater overall operating efficiency to the equipment.
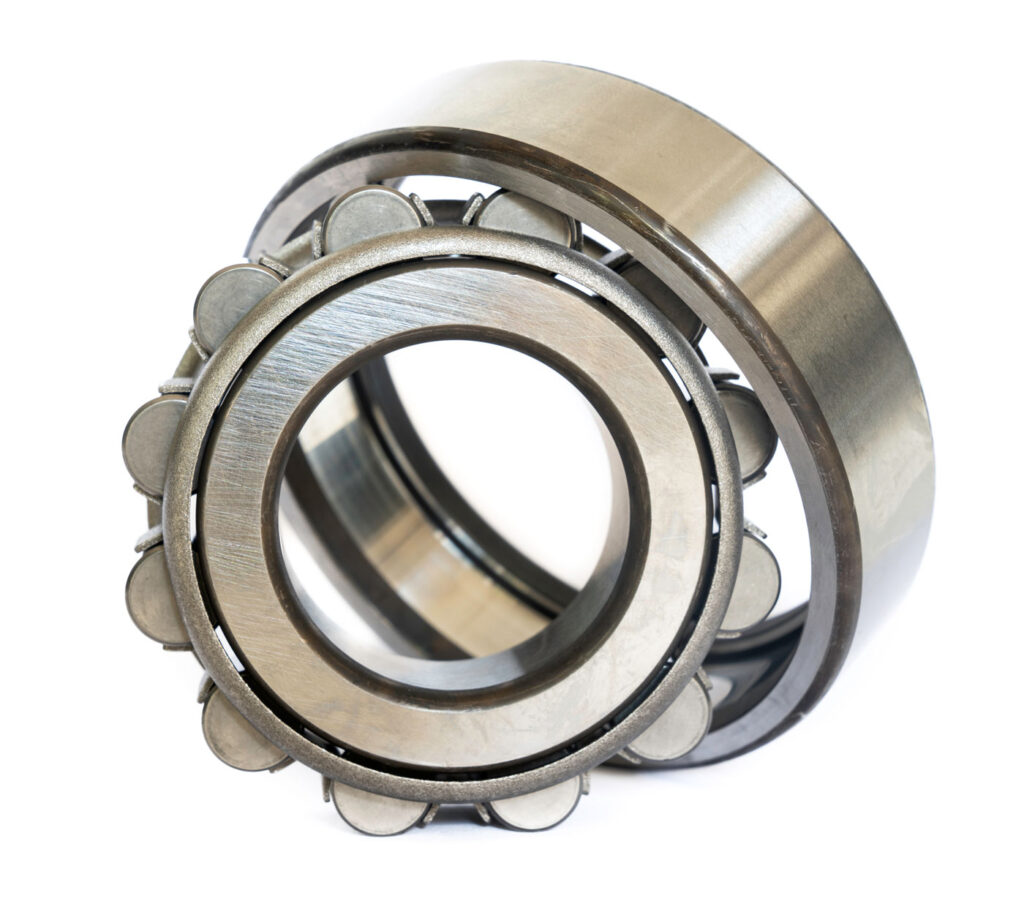
Integrated Lubrication Pathways
In addition, cylindrical roller bearings are designed with built-in lubrication channels. It is designed to reduce the maintenance requirements of the bearings, ensure that the lubricant can be evenly distributed in the key parts of the bearings, and ensure that the rollers and raceways are well lubricated. This built-in lubrication mechanism reduces the lubrication operations required and the frequency of maintenance.
Reduced Friction and Long Life Of Cylindrical Roller Bearings
Optimized Surface Finish
The raceways and roller surfaces of cylindrical roller bearings are processed with high precision to effectively reduce the friction coefficient. The rollers are arranged in parallel, and spacers or spacers are installed between the rollers. This design not only prevents the rollers from tilting but also reduces the friction between the rollers and the increase in rotational torque.
Improved Thermal Stability
In high-speed operation, friction can cause temperature rise, resulting in changes in the expansion size of machine components or performance degradation. Cylindrical roller bearings can use special materials and designs to keep the temperature rise lower at high speeds, extending their life. These designs improve the thermal stability of bearings and are suitable for high-speed equipment such as turbines and compressors. Split cylindrical roller bearings are a typical example. It features non-contact sealing and improved load-carrying capabilities to handle higher speeds and temperatures.
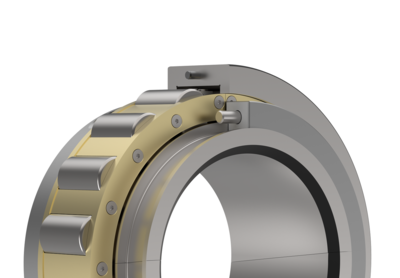