2022 Bearing Type Selection Guide
Bearing Selection Guide
2022 latest bearing type selection guide. To make the mechanical device play the expected performance, choosing the most suitable bearing is very important. In addition, the selection of bearings requires research from many factors and evaluation of the piece of bearings from various angles. Although there are no special requirements, the general sequence is as follows.
- Master the operating conditions of mechanical devices and bearings, etc.
- Clear requirements for bearings
- Select the bearing
- Selection of bearing arrangement
- Select bearing size
- Selection of bearing specifications
- How to install the selected bearing
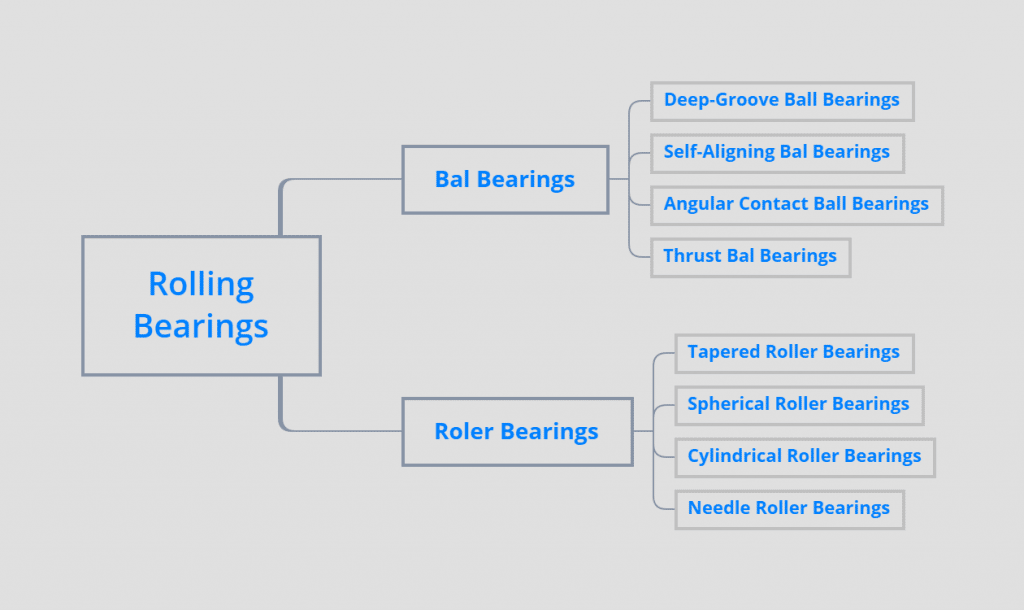
Bearing operating conditions and environmental conditions
Correctly grasping the location of the bearing in the mechanical device and the conditions of use and environmental conditions are the prerequisites for choosing a suitable bearing. For this, it is necessary to obtain the following data and information:
- Function and structure of the mechanical device
- Where the bearing is used
- Bearing load (size, direction)
- Rotation speed
- Vibration, shock
- Bearing temperature (ambient temperature, temperature rise)
- Ambient atmosphere (corrosiveness, cleanliness, lubricity)
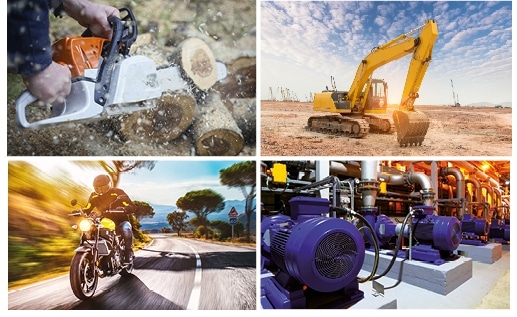
The choice of bearing arrangement
Generally, the shaft is supported by two bearings in the radial and axial directions. At this time, the bearing on one side is called the fixed side bearing, the effect of relative axial displacement between. The other side is called the free side, which only bears the radial load and can move relative to the axial direction, which solves the problem of shaft expansion and contraction caused by temperature changes and the clearance error of installing the bearing.
For fixed-side bearings, it is necessary to select a bearing that can move the rolling surface in the axial direction (such as cylindrical roller bearings) or on the assembly surface (such as radial ball bearings). When the fixed and free sides are the same on relatively short shafts, use bearings that only move in one direction (such as centripetal thrust ball bearings).
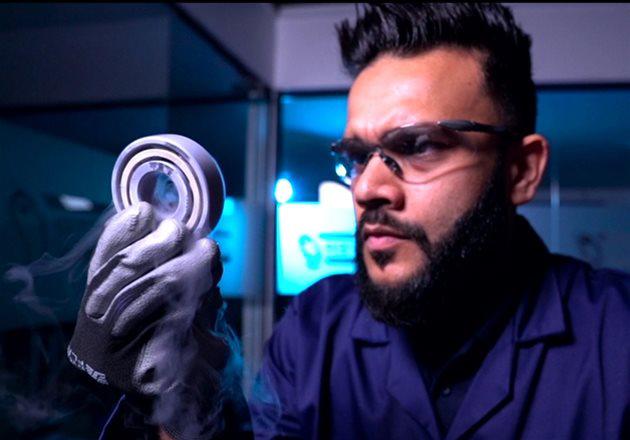
Bearings and Its Types
Generally, all types of machinery are provided with supports for rotating shafts; the supporting device is known as a bearing. In other words, a bearing is a machine element that constrains relative motions and is used to reduce the friction between moving parts.
Bearing employs to support, guide, and restrain moving the element. This is a stationary member, and it carries the load.
The shaft supported by the bearing is known as the journal, a mov ng member. Bearings are classified according to the type of operation they do.
∙ The motions allowed, or
∙ to the directions of the loads or forces applied to the parts.
The typical applications of bearing s are:
- Shafting in wor shops,
2. Spindles of a machine tool such as a lathe, drilling, milling machines, etc.
3. The crankshaft of engines, axles of automobiles, etc.
Classification of Bearings
There are three main classifications of bearings, according to the direction of load viz.,
- Journal or radial bearing,
2. Footstep bearing,
3. Thrust or collar bearing.
∙ A journal or radial bearing supports the shaft at a right angle to the shaft axis.
∙ A footstep or pivot bearing support shaft parallel to the shaft axis and the end of the shaft rests on the bearing surfaces.
∙ A thrust or collar bearing supports the shaft subjected to end or axial thrust.
The surfaces of the bearing are generally flat or c cylindrical. And they may consist of nonferrous metal surfaces known as bushes or hardened steel races supported by steel balls r rollers. In the above case, the bearing is known as bush bearings, and the latter is known as a ball or roller bearings.
Bearing types
Following are the different types of being rings:
- Bush earing
2. Plummer Block
3. Thrust Baring
- Foot Step Bearing
Rolling contact or Anti-friction Baring
- Ball and Roller Bearings
Read also: Gear Terminology: Basic Terms Used In Gear
Bush Bearings
The simplest type of bush bearing is shown in the figure. It consists of a cast-iron bearing block and a brass or gunmetal bush. In these bearing types, The base plate of the bearing block provides holes for bolting down the bearing in position.
At the top of the bearing, a counterboring oil hole passes through the block and bush to the action of theft and the bush lubrication.
It is used for the shaft, which carries light loads and rotates at s ow speeds. In this type of solid bearing, the post may introduce and removed wisely.
Read Also: Nuts and Bolts [The Complete Guide]
Plummer Block
A pedestal bearing or more Plummer block is used when a long shaft requires support at an intermediate point.
It consists ts of:
- A cast-iron pedestal or blocks with sole,
2. Tow split gum metal or ushes,
3. A cast-iron cap and two square-headed bolts fastening the cap and the block together.
A projecting snug in the bottom bush, fitting in the corresponding hole in the body or block, prevents the rotation. The brush is prevented from moving along the length of the shaft by two collars at the sides. It is made of two halves to help.
∙ Placing and removal of the post in and from the bearing.
∙ Change for wear in the bushes, and
∙ Renewal of the bushes.
In a bu h bearing. There is a rubbing action between the outer surface of the shaft and the inner surface of t e bearing. And the resulting friction minimizes by the presence of a lubrication oil film.
Ring oiling may be considered the safest and most efficient line shafting type under normal service conditions.
Read also: Screw Thread Terminology and Types of Screw Threads
Thrust Bearings
In thrust bearing, the bearing pressure will be axial. The axis of the shaft may have vertical or horizontal.
Suppose the shaft axis is vertical; the thrust bearing is known as the footrest p bearing. If the shaft axis is horizontal, the thrust bearing is known as a roller bearing.
Read Also: Clutch: 9 Different Types of Clutches and How they Work
Foot Step Bearing
The figure shows a simple type of footrest p bearing. It is suitable for supporting a vert cal shaft. It consists of a cast-iron block and a gunmetal bush. The lower end of the post rests on a steel disc having open seating.
In this type of bearing, the disc is prevented from rotating along the shaft and the shaft by partially inserting the pin into the bearing seat and partially inserting the disc. The bushing prevents rotation with the post by a tight fit provided at the neck below the collar.
The main disadvantages of this type of bearing are that it is difficult to achieve adequate l ration. This type of bearing is generally used for slow-speed shafts carrying light loads.
Generally, the vertical shaft is uncommon in the ordinary transmission of power. But they often occur on machine practice in machine tool turntables, textile machinery, etc.
Rolling Antifrictionti-friction bearings
It is well-known that a smooth rounded surface will roll over a similar surface more than when it’s sliding. This phenomenon employs hard chrome steel balls or rollers to run in special design cages to provide bearings with low friction loss.
In these bearing types, the motion between the shaft and the bearing surface is pure rolling. Since the rolling friction is much less than the sliding friction, this type is kantifrictionntifriction bearing.
The twantifrictionntifriction bearing
- Ball Bearing
2. Rolling Bearing.
The outstanding featantifrictionntifriction bearings are their low starting frictions, which will be practically the same while running. This renders their application particularly suitable for machinery which has to start, stop and restart frequently.
Read Also: Clutch – Its Main Parts and Working Principle of Clutch
Ball and Rolling Bearings
The figure shows the simplest type of ball and roller g bearing. It consists of a rigid steel ball and rolling, between two suitable grooves, hard steel rings, known as races.
In this type of bearing, the ball and rolling are retained in positions by operators. These are known as cages, usually made of brass. The inner race should be of ‘drive fit’ on the shaft to a rota. The outer race fits into the housing and does not rotate.
A ball and rolling being free to rotate, the action in them is not that of rubbing but of rolling between the balls and rolling and t eir races. Since the rolling friction is much less than the sliding friction, the ball and rolling bearing are antifriction bearings.
Rolling bearings maintain accurate alignment of every part over a long period and can carry the heavy mome tary load. This renders them suitable for machinery which requires frequent starts and stops. Rolling makes the line contact with their races, while balls make poi contact. Rolling, thus, has a higher load-carrying capacity.
At the point (or line) of contact between a ball (or rolling) and its races, the pressure intensity is as great as film lubrication, as usually understood is impossible. Lubrication is necessary to protect the polished surface from rust and help exclude the fore in the matter. Pure mineral grease is so generally used.
Read Also: Chain Drives and Types Of Chains
Advantages of Rolling Contact earing
- Starting and running friction is negl gible.
2. Can be used for radial and thrust load.
3. Requires minimum lubri action.
4. Suitable for high speeds.
5. Serves for long life.
Disadvantages of Rolling Contact Bearings
- High initial cost.
2. More liable to shock loads.
3. Requires a very high precision machining of the bearing h using.
4. Not suitable for heavy loads.
5. Worn-out parts cannot be repaired; the only entire bearing unit will be replaced.