Where the Fixed End of Motor Bearings Be Placed Front or Back?
Introduction
When designing the structure of a horizontal motor, one crucial decision is where to position the fixed end of motor bearings—either at the front (drive end, where the shaft extends to connect with external loads) or the back (non-drive end).
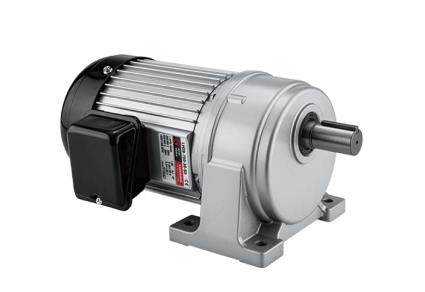
This choice affects how the motor handles loads, manages thermal expansion, and eases maintenance.
Let’s break it down step by step to help you make the best decision for your motor design.
Contents
hide
Understanding the Basics: Drive End vs. Non-Drive End
First, let’s clarify the terms:
-
Drive End (DE): The front of the motor where the shaft extends to connect with external loads like couplings or pulleys.
-
Non-Drive End (NDE): The back of the motor, typically where the fan or other components are located.
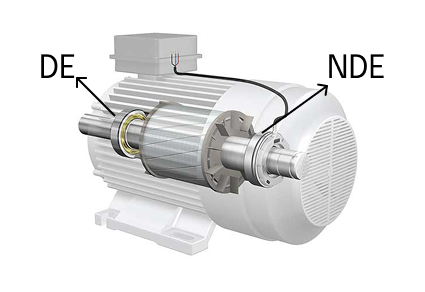
In a horizontal motor, the bearings at both ends support the rotor, but their roles differ based on the loads they handle:
-
Radial Loads: These are forces perpendicular to the shaft, like the weight of the rotor or external loads from pulleys. The DE usually bears more radial load because it’s closer to the external connections.
-
Axial Loads: These are forces along the shaft’s axis, often from thermal expansion or external thrusts. The fixed end bearing handles these axial loads, while the floating end allows the shaft to expand and contract.
So, the fixed end is critical for axial positioning—it keeps the shaft in place along its length.
The floating end, on the other hand, allows for movement due to heat expansion.
Why Does the Placement of the Fixed End of Motor Bearings Matter?
The placement of the fixed end affects three main areas:
-
Load Distribution
-
Thermal Expansion Management
-
Maintenance Ease
Let’s explore the pros and cons of placing the fixed end at the DE versus the NDE.
Option 1: Fixed End at the Drive End (DE)
Pros
-
Minimizes Axial Movement at the DE: Since the fixed end is at the DE, thermal expansion of the shaft happens mostly toward the NDE. This keeps the DE’s position stable, which is great for equipment connected to the motor (like pumps or fans) that might be sensitive to axial shifts.
-
Better for Precision Applications: If your motor drives equipment that requires precise alignment, keeping the DE stable is a big advantage.
Cons
-
Larger Bearing May Be Needed: The DE bearing has to handle both higher radial loads (from external connections) and axial loads. This might require a larger, more expensive bearing.
-
Maintenance Challenges: Fixing issues at the DE often means disassembling the entire motor, which can be time-consuming and costly.
Option 2: Fixed End at the Non-Drive End (NDE)
Pros
-
Balanced Bearing Sizes: The NDE typically bears less radial load, so placing the fixed end here might allow for smaller bearings at both ends, potentially lowering costs.
-
Easier Maintenance: Accessing the NDE is often simpler—just remove the end cover and fan—making repairs quicker and less disruptive.
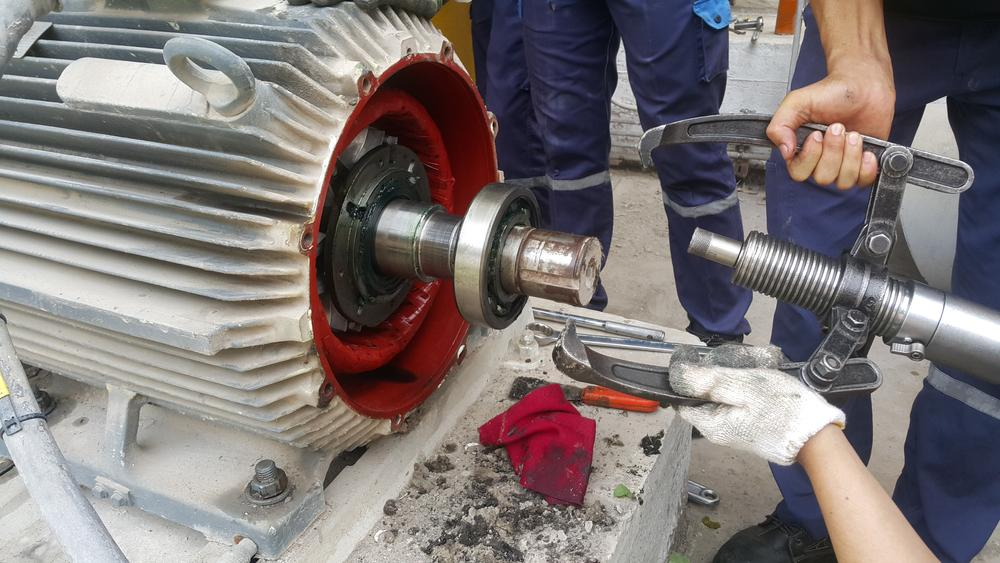
Cons
-
More Axial Movement at the DE: With the fixed end at the NDE, thermal expansion pushes the shaft toward the DE, causing more axial shift there. This could affect connected equipment, especially if it’s not designed to handle such movement.
-
Requires Careful Design: You’ll need to ensure that the coupling or connection at the DE can accommodate the extra axial play, particularly when the motor heats up or cools down.
So, Which One Should You Choose?
The answer depends on your specific application:
-
Choose DE as the fixed end if:
-
Your motor connects to equipment that can’t tolerate much axial movement.
-
Precision and stability at the DE are more important than cost or maintenance ease.
-
-
Choose NDE as the fixed end if:
-
Cost savings from using smaller bearings are a priority.
-
Maintenance access is a concern, and you can manage the axial movement at the DE with proper coupling design.
-
-
Quick Tip: Always check the requirements of the connected equipment. If it’s sensitive to axial shifts, prioritize stability at the DE. If not, you might save on costs and maintenance by fixing the NDE.
Conclusion: It’s All About Balance
There’s no one-size-fits-all answer to whether the fixed end should be at the front or back of the motor. It’s a trade-off between load handling, thermal management, and maintenance needs. By understanding how each placement affects your motor’s performance and the equipment it drives, you can make a smart, informed decision.
So, next time you’re designing a motor, ask yourself: What matters most—stability, cost, or ease of repair? Let that guide your choice, and your motor will thank you with smooth, reliable operation!
If you also have some questions about fixed end of motor bearings, contact us any time!