How to prolong the service life of slewing ring bearings
The slewing ring includes an inner ring and an outer ring, one of which usually contains a gear. Together with the connecting holes on the two rings, they achieve optimized power transmission through simple and quick connections between adjacent machine parts. The bearing raceways are designed together with rolling elements and cages or spacers to withstand loads in any direction, alone or in combination.
TFL produces standard and custom slewing bearings in various designs, with outer diameters ranging from 0.1 to 18 m to meet the needs of specific applications.
TFL BEARING is an authorized SKF distributor. For more information about SKF Kaydon slewing ring bearings, please refer to Kaydon Bearings.
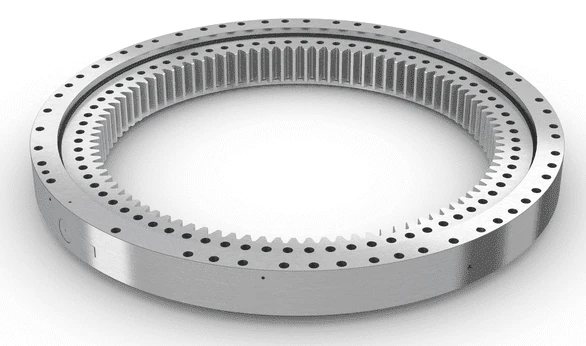
The main advantages and differences of precision slewing bearings
Slewing ring bearings have many unique advantages over other ball bearings and roller bearings, especially heavy-duty applications requiring great freedom of movement.
Multifunctional load spectrum of slewing ring: The slewing ring provides 360-degree joint support for complex load support systems, allowing simultaneous movement on multiple axes.
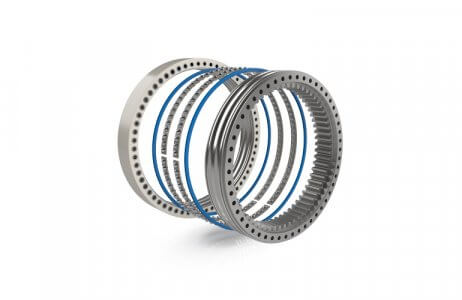
Shaftless design: The slewing ring is designed to operate without a shaft or main shaft, thereby enhancing bearing movement and leaving room for additional operating parts.
Carrying capacity: The slewing ring bearing is designed to handle the movement of heavy loads with high efficiency.
Ideal stiffness: Although they are designed to promote a wide range of motion, slewing ring bearings exhibit high material stiffness to ensure adequate support in rigid bearing applications.
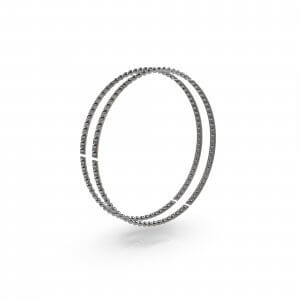
Low friction: The low friction and freedom of movement of the slewing ring bearing are particularly valuable, which improves the process efficiency and, at the same time, increases the service life of the bearing and surrounding equipment.
Extended service life: Slewing ring bearings provide highly durable, low-friction load-bearing options, reducing stress and friction on the bearing and interacting components. Reduced equipment wear helps to extend the life of the bearing and the entire system.
Application of precision slewing bearing
The versatility and efficiency of slewing bearings make them very suitable for various industries and applications, from military and defence equipment to manufacturing and transportation. Common applications include:
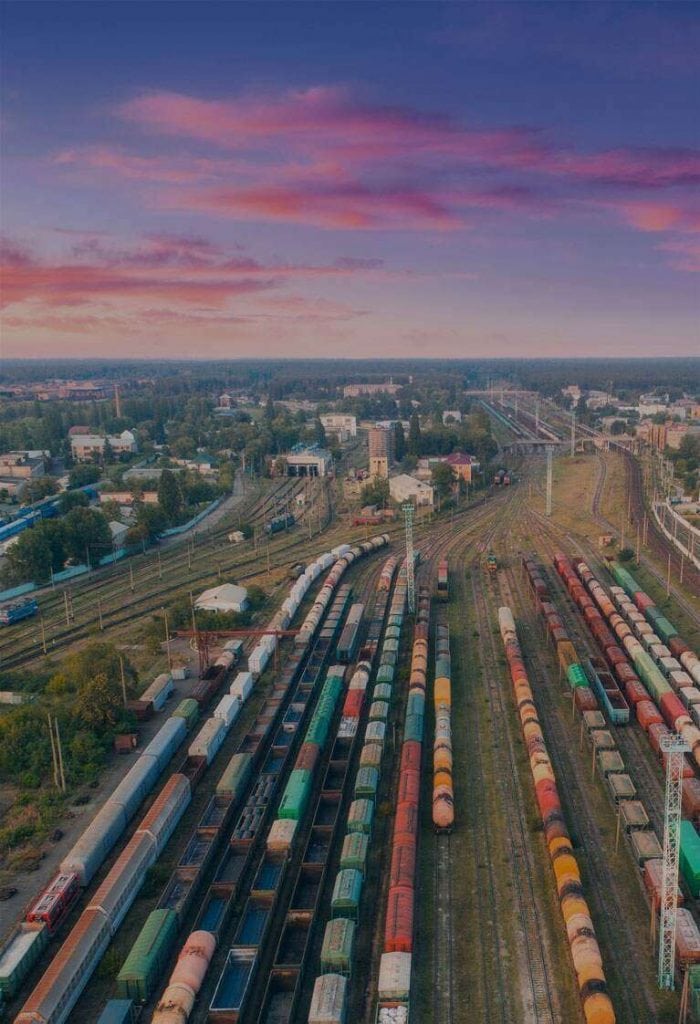
Military and national defence: Slewing ring bearings are usually used in military and national defence equipment that must guide heavy loads with high precision. They can be found in missile launchers, tank turrets, and optical equipment.
Construction: The construction industry benefits from slewing bearings, especially in load-bearing and lifting applications, such as lifts, cranes, hydraulic excavators, and drilling machines.
Bottling technology: The 360-degree rotation of the slewing ring makes it particularly suitable for industrial bottling applications, including sterilization, rinsing, capping, and labelling functions.
Mining: Slewing bearings are often used in mining and tunnelling, and the equipment must be able to move freely under heavy loads.
Transportation: Trains, trams, and subways often use slewing bearings to facilitate vehicles’ free and easy movement.
Tools and processing: Slewing ring bearings are usually used to promote the movement of precision machine tools. They allow free multi-axis movement of machine tool spindles in precision milling and turning applications.
Bearing maintenance and maintenance
How to prolong the service life of slewing ring bearings?
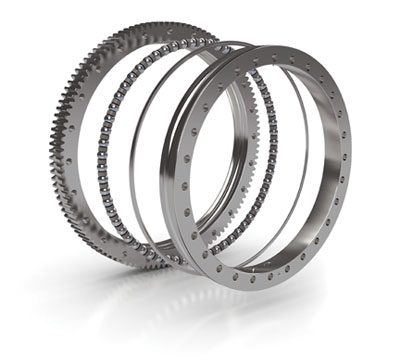
Premature failure is a common fate for large-diameter (e.g., 8″ to 10′) bearings in heavy-duty applications where rotations are frequent. In big rotating equipment, such as cranes, excavators, and tunnel boring machines, a slewing ring bearing must simultaneously handle a complex load spectrum covering diverse combinations of thrust, radial, and tilting moment loading.
Fortunately, there’s an easy way to protect your investment in these custom-engineered bearings. It’s called regular maintenance, and it can prevent 96% slewing ring-bearing failures. To maximize bearing life, follow these four tips – raceway and gear lubrication, torque checks on bolts, and seal inspection – and be alert for four warning signs of potential bearing problems.
Bearing Lubrication
A bearing should be lubricated at regular intervals with heavy-duty, extreme-pressure grease. Apply a liberal shot to the fittings around the bearing’s circumference at the interval recommended in the operator’s manual.
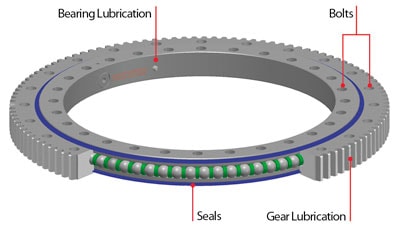
Slowly-rotating equipment or oscillating applications (e.g., backhoes, excavators, cranes) should be re-lubricated about every 100 hours of operation. More frequent lubrication – every day or even every eight hours – may be needed on equipment that moves rapidly or rotates continuously, such as trenchers and boring machines.
While adding grease, the bearings should be rotated to spread the grease throughout. Pump it in until you see the old grease squeeze past the seal; this is called purging. Purged grease carries contaminants out of the bearing. Rub some between your thumb and forefinger… if you feel grit or metal chips, you may have a bearing problem.
Grease tends to dry out over long periods of time, allowing condensation to form within a bearing. You can avoid this by introducing grease at least every six months, even when the equipment is sitting idle.
Gear Lubrication
Most large bearings have gear teeth that require lubrication, and those requirements are different from those for the bearing itself. Since the meshing action of the teeth tends to squeeze out lubricant, gears should be lubricated every eight hours on slow-rotating or intermittently rotating equipment and more often on rapidly or continuously rotating equipment. Small amounts of grease should be introduced at the point of mesh between the gear and pinion.
Seals
The seals on the bearing should be visually inspected periodically to be sure they are intact. Many people overlook the importance of seals, but they aid considerably in preventing bearing raceway contamination.
Bolts
A torque check on bolts should be part of any routine maintenance procedure. The frequency of these checks depends on the severity of the service. Vibration and shock tend to loosen bolts, but periodic torque checks and tightening will help maintain the proper preload level.
Mounting bolts should be torqued to the proper level and checked periodically to ensure proper pre-tension. Improperly pre-tensioned bolts can fail, causing damage to equipment and, even more importantly, injuries to workers.
Bolt creep is another factor that should be monitored. Tightened bolts tend to creep or elongate over a period of time, reducing preload. Elevated temperatures can also increase bolt creep, so consider this when developing a torque-check schedule.
4 Warning Signs of Bearing Problems
Regular maintenance goes a long way toward preventing premature failure, but even the most faithfully maintained bearings will eventually show signs of wear. To extend their life, look for these common signs and take corrective action as indicated.
Play or clearance in the bearing often signifies that a raceway is worn. A new bearing is assembled with a specific amount of clearance to compensate for slight out-of-flatness in a mounting structure. Wear can increase this clearance dramatically. In machinery with a boom, free play magnified over the length of the boom allows it to rock back and forth under load, reducing the ‘stiffness’ in the extended boom. Check bearing clearance with a dial indicator that measures how much the structure tilts when the boom is loaded.
Grinding, popping, or clicking noises from the bearing typically mean there could be inadequate lubrication and/or excessive wear in the raceway or lose bolts. As noted previously, greasing the bearing and purging lubricant is a good way to check for metal particles.
An increase in torque or binding can mean uneven wear in the raceway. If the turning torque of the bearing increases substantially or the bearing has tight spots, the load is probably unevenly distributed. With excavators, for example, the operator may sense a resistance to swing and find that the upper boom swings an inch or two past the point where it should stop. In advanced stages of wear, the bearing will pop and crack as the machine digs and swings.
Dimpled raceways are typically the result of overloading the bearing or repetitive, heavy loads. Even slight overloads can dimple a bearing race, and a dimple that starts at 1/1000th of an inch will almost always get bigger. The same goes for uneven loads. Lifting with a boom and undercarriage in the same position every time (such as curbside digging with an excavator) can dimple the bearing race near the uneven load. If possible, change the angle of approach from job to job.
Less Wear Means Less Expense
By monitoring the symptoms of bearing wear and regular preventive maintenance, you can significantly reduce the chances that a bearing will fail prematurely. This, in turn, minimizes expense because it keeps equipment working productively, avoiding breakdowns that lead to costly downtime and repairs.
Longer bearing life also means, of course, that bearings can be replaced less often, stretching budgets further. And when the time for replacement comes, consider having your old bearings remanufactured instead of buying new ones. Well-maintained bearings can typically be repaired for less than half the cost of a new replacement if repaired before they fail.
Contact: Candice
Email: info@tflbearing.com
MP/Whatsapp: (86)15806631151
WeChat: 15806631151