Vibration Analysis in Cylindrical Roller Bearing Detection
Introduction
Machines need parts called bearings to move smoothly. Cylindrical roller bearings are a special type of bearing used in lots of machines. If these bearings get damaged, the machines can break down. One way to check if bearings are okay is by looking at their vibrations. This is called vibration analysis.
By measuring vibrations, you can catch problems early—before they turn into expensive disasters. Let’s break down how this works and why it matters for your equipment.
Contents
hide
What is Vibration Analysis and How Does It Work?
The Basics of Vibration Analysis for Cylindrical Roller Bearings
Vibration analysis is like a “checkup” for machines. Every machine vibrates a little when it runs, but those vibrations have a pattern. By analyzing vibration patterns, you can detect early signs of wear, misalignment, or other problems. In this way, you can find the potential risk before you set the bearings on your equipment.
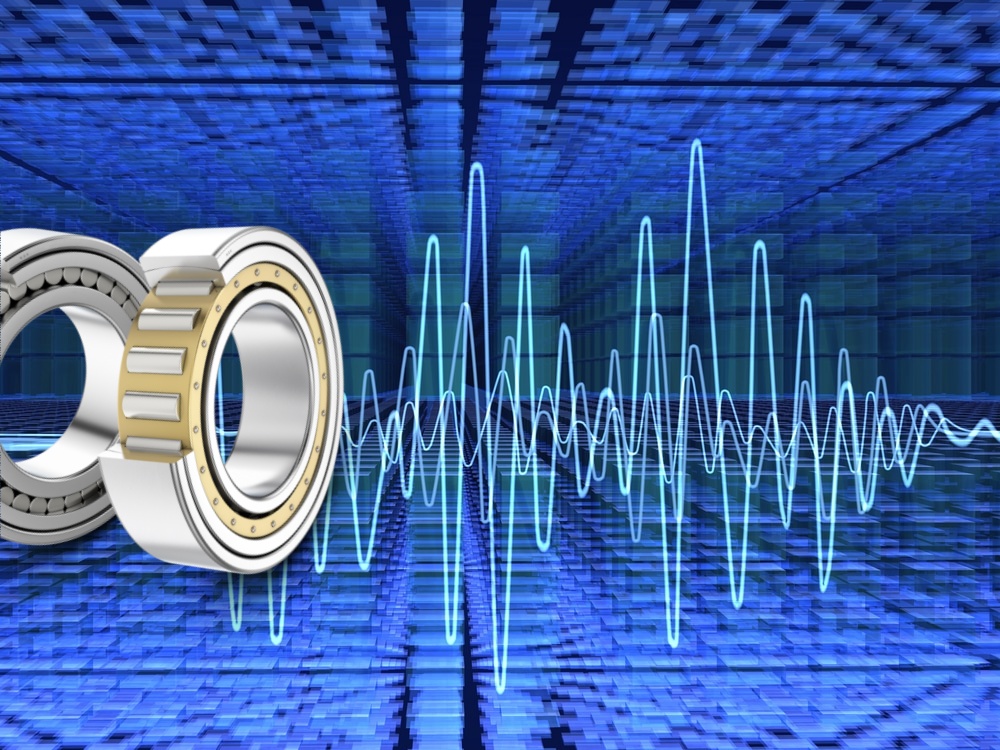
Key Sources of Vibration in Cylindrical Roller Bearings
The vibration in cylindrical roller bearings are mainly caused by the following sources:
-
Contact Between Rolling Elements and Raceways: As rolling elements move along the raceways, they inevitably generate vibrations. This is the primary source of vibration in cylindrical roller bearings.
-
Assembly Errors: Incorrect installation or improper fit between the bearing and the shaft or housing can introduce additional vibrations.
-
Fluctuating External Loads: Uneven load distribution or sudden impact loads can cause vibrations to increase in cylindrical roller bearings.
-
Poor Lubrication: If there isn’t enough oil or if the grease is worn out, it can cause more friction. This makes vibrations worse and wears things out faster.
(Reference: Schaeffler Group’s guide, An Overview of Bearing Vibration Analysis by Dr. S. J. Lacey)
How Vibration Analysis Works for Cylindrical Roller Bearings
Vibration analysis tools help identify changes in vibration patterns, allowing you to detect issues early. For example:
-
Normal Vibrations: A smooth, steady hum indicates healthy cylindrical roller bearings.
-
Abnormal Vibrations: Jerky spikes or uneven rhythms suggest problems such as bearing wear, misalignment, or lubrication issues.
By monitoring these patterns, you can distinguish if your cylindrical roller bearings are in bad performance.
Tools You’ll Need for Vibration Analysis of Cylindrical Roller Bearings
Vibration analysis doesn’t require a Ph.D., but having the right tools is essential to effectively monitor and diagnose issues in cylindrical roller bearings. Here’s a breakdown of the tools you’ll need and how they help:
Essential Tools for Analyzing Cylindrical Roller Bearings
-
Sensors: Sensors are essential for vibration research. These devices attach to the machine with cylindrical roller bearings and work like mics to catch vibrations. They sense even the small changes in vibrations, which makes them crucial for finding problems early.
-
Software: After the sensors gather vibration data, special software turns it into simple plots and charts. You can use free or low-cost apps like SpectraQuest or smartphone tools to examine data and spot issues in cylindrical roller bearings.
-
Your Senses: While technology plays a significant role, don’t underestimate the power of your own senses. For example:
-
Hearing: A grinding or rumbling noise often indicates a failing cylindrical roller bearing.
-
Touch: Excess heat around the bearing housing can signal friction or lubrication issues.
-
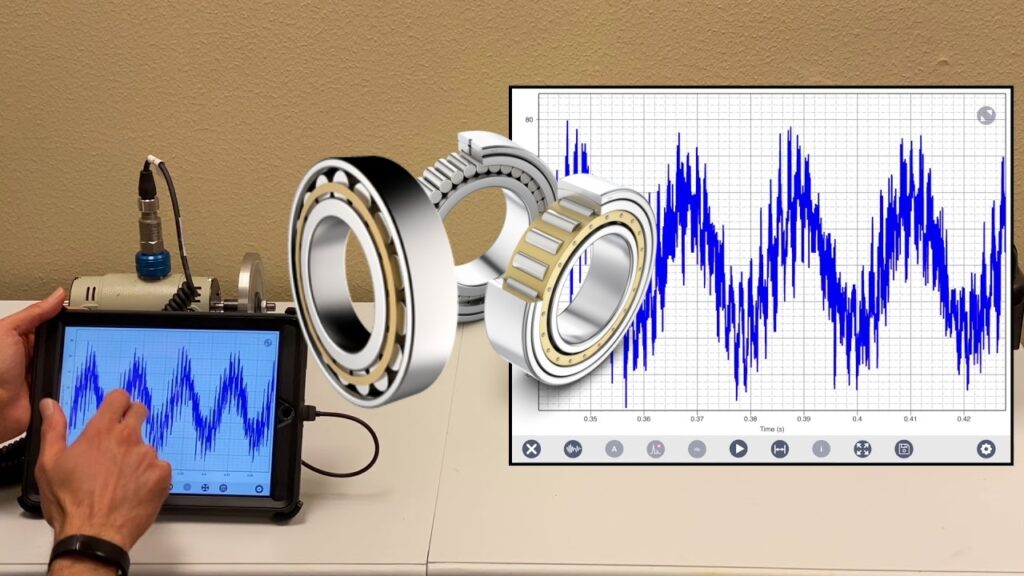
How to Read Vibration Data for Cylindrical Roller Bearings
Once you’ve collected vibration data using the tools above, the next step is interpreting it. Here’s a step-by-step guide to help you understand what the data means and how to act on it:
-
Compare to Baseline: Every machine has a “normal” vibration level, known as the baseline. If your readings show vibrations 20% or more above this baseline, it’s time to investigate further. For cylindrical roller bearings, even small deviations can indicate early signs of wear or misalignment.
-
Look for Patterns: Vibration graphs often reveal specific patterns that point to particular issues:
-
High-frequency spikes: These sharp peaks might show issues such as cracked rollers, not enough grease, or surface damage in cylindrical roller bearings.
-
Uneven waves: Irregular vibration patterns often suggest misaligned bearings or uneven load distribution.
-
-
Act Fast: Early detection is key. Small changes in vibration patterns today can escalate into major failures tomorrow. By addressing issues promptly, you can extend the lifespan of your cylindrical roller bearings and avoid costly downtime.
Benefits of Vibration Analysis for Cylindrical Roller Bearings
Early Detection of Bearing Wear or Damage
Cylindrical roller bearings work hard, but tiny cracks or worn rollers can sneak up on you. Vibration analysis catches these issues before they wreck your machine. For example:
-
A small crack in a roller might only cost $20 to fix if caught early.
-
If ignored, that crack could shatter the bearing, costing $500+ and halting production.
Reducing Unplanned Downtime
Machines breaking down unexpectedly is like a flat tire on a road trip—it ruins your plans. Vibration analysis helps you:
-
Schedule repairs during slow periods.
-
Avoid “surprise” breakdowns that stop your work.
Saving Money on Repairs
Replacing one bearing is cheaper than replacing a whole machine. Plus, fixing issues early means:
-
Less damage to nearby parts (like shafts or housings).
-
No rush fees for emergency repairs.
Common Problems Detected in Cylindrical Roller Bearings
Misalignment Issues
If bearings aren’t perfectly aligned, they’ll vibrate unevenly. Imagine a car wheel out of balance—it shakes the whole vehicle. For cylindrical roller bearings, misalignment causes:
-
Faster wear on rollers and raceways.
-
Extra stress on the machine’s frame.
How vibration analysis helps: It detects uneven vibration patterns, so you can realign the bearings before they fail.
Lubrication Failures
Bearings need grease to stay cool and quiet. No grease = grinding metal-on-metal. Signs include:
-
High-pitched squealing noises.
-
Overheated bearings (use a thermal gun to check).
How vibration analysis helps: Dry bearings create high-frequency vibrations. The software flags these as “lubrication issues.”
Bearing Fatigue or Cracks
Even strong bearings get tired over time. Fatigue cracks often start small and grow slowly. Vibration analysis spots these by:
-
Noticing changes in vibration “harmonics” (like a guitar string going out of tune).
-
Alerting you to replace the bearing before it fails catastrophically.
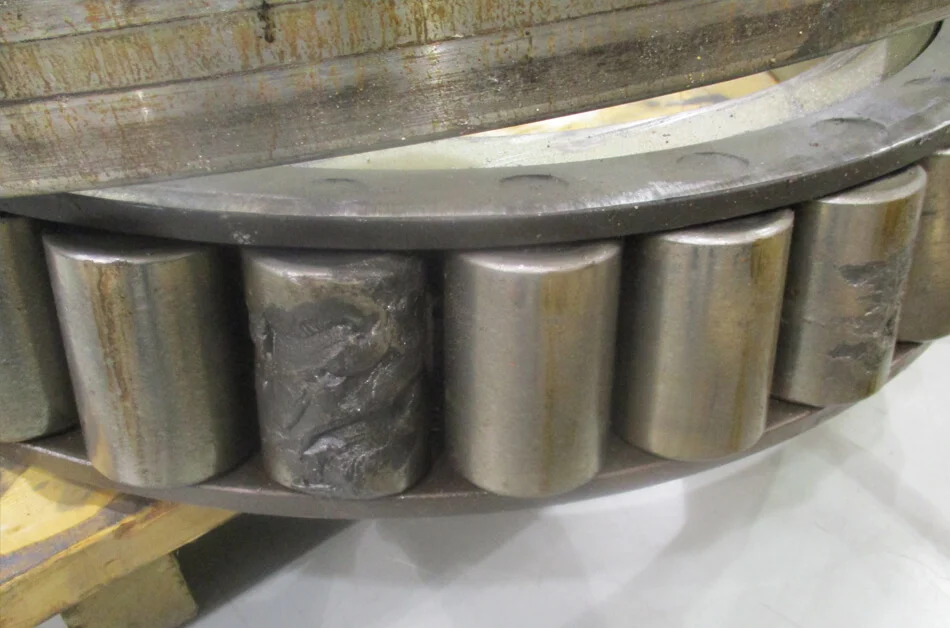
How to Perform Vibration Analysis on Cylindrical Roller Bearings
Step-by-Step Setup for Vibration Testing
-
Clean the area: Dust or oil on the machine can mess up sensor readings.
-
Attach sensors: Place them close to the bearings (usually on the housing).
-
Run the machine: Let it operate normally for 10–15 minutes while sensors collect data.
Best Practices for Accurate Data
-
Test regularly: Check bearings every 3–6 months (or more for heavy-use machines).
-
Record baseline data: Know what “normal” looks like for your equipment.
-
Check multiple points: Test different spots on the machine to rule out other issues.
Interpreting Vibration Patterns
-
Low-frequency vibrations: Often mean looseness or misalignment.
-
High-frequency spikes: Likely cracks or lubrication problems.
-
Side note: If you’re unsure, compare your data to online guides or ask a specialist.
Best Practices for Maintaining Cylindrical Roller Bearings
Regular Inspection Schedules
Don’t wait for problems! Add these to your routine:
-
Monthly: Quick visual checks for rust, leaks, or loose parts.
-
Quarterly: Basic vibration tests and grease top-ups.
-
Yearly: Deep inspections (disassemble bearings if needed).
Combine Vibration Analysis with Other Checks
Vibration tools are great, but pair them with:
-
Temperature checks: Use a thermal gun to spot overheating.
-
Sound checks: Listen for grinding or rattling noises.
-
Visual checks: Look for cracked seals or grease leaks.
Train Your Team to Spot Early Signs
Teach workers to:
-
Recognize unusual noises (e.g., “This machine sounds like a coffee grinder!”).
-
Report vibrations that “feel different” (e.g., more shaking than usual).
-
Use simple tools (like a screwdriver pressed to the ear) to listen for bearing noise.
Conclusion
Cylindrical roller bearings are workhorses, but they need a little love. Vibration analysis is a simple, no-nonsense way to keep them running smoothly—saving you time, money, and stress.
At TFL Bearings, we engineer our bearings to last, but even the toughest parts need a checkup now and then.
Need Bearings That Work as Hard as You Do? Explore TFL Bearings’ range of durable cylindrical roller bearings. Got questions? Our team’s just a click away—let’s keep your machines running!